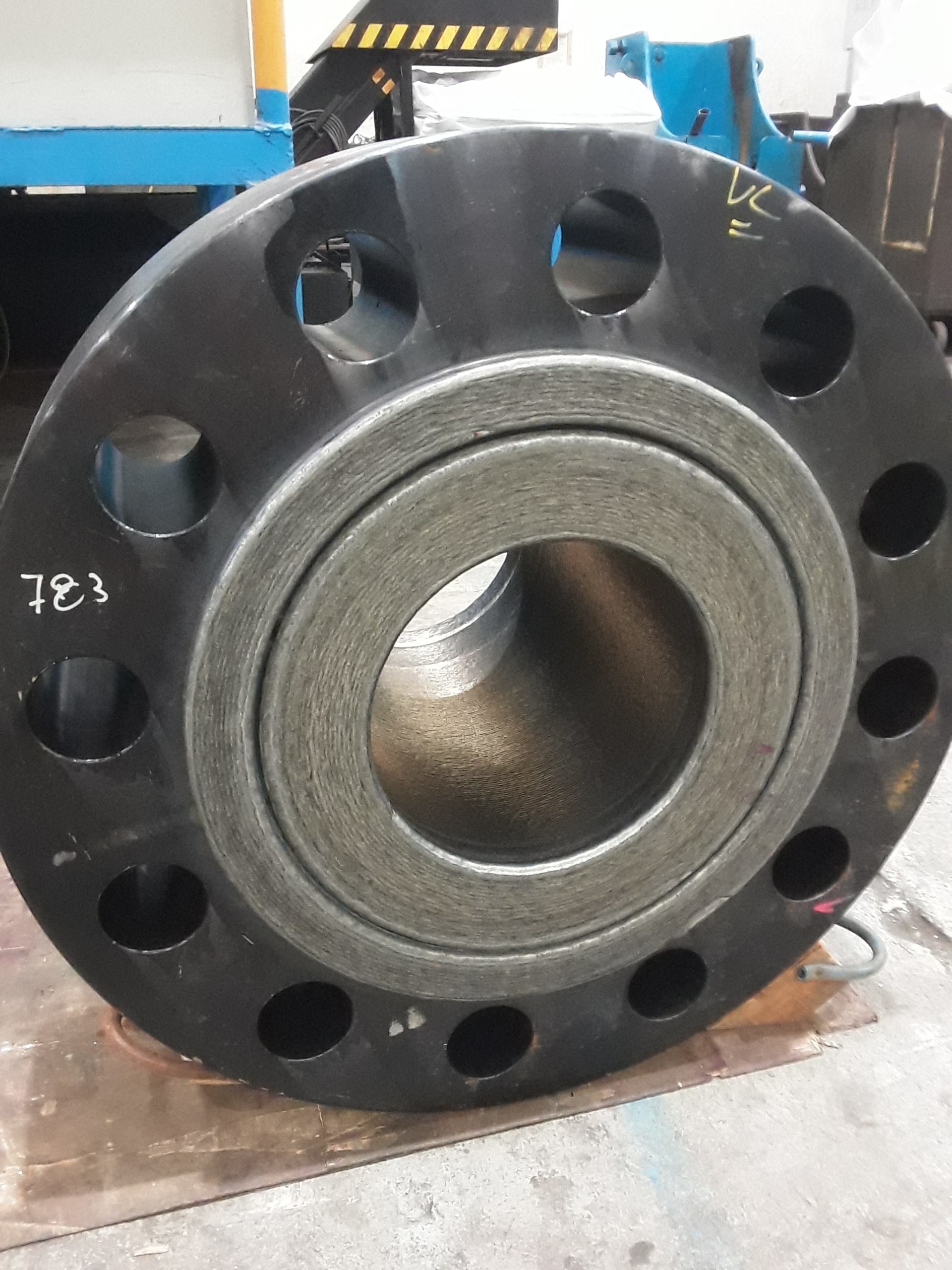
Визначення та використання Holy Flagge
Визначення та використання Holy Flagge наступні:
визначення:
Охоплений фланець - це фланець, який накладає накладку на фланці. Ця обробка часто використовується для поліпшення корозії та зносу фланця, що дозволяє використовувати його в суворих умовах.
використання:
- Антикорозійний захист : Фланець з прикріпленням запобігає корозії, додаючи шар стійкого до корозії матеріалу, наприклад, нержавіюча сталь або нікелевий сплав, на поверхню фланця. Це особливо важливо для трубопроводів та обладнання, що використовуються в таких галузях, як хімічна речовина, нафта і газ.
- Підвищення стійкості : Додаючи шар стійкого до зносу матеріалу, Охоплений фланець може продовжити термін служби обладнання та зменшити витрати на обслуговування.
- З'єднання та ущільнення : Кладовий фланець - це з'єднувальна компонент у трубопровідній системі і використовується для підключення труб, клапани, насоси та інше обладнання. Він ущільнюється через болти та шайби, щоб забезпечити безпечну роботу системи.
- Стандарти і технічні умови : Клад Фланг дотримується міжнародних та національних стандартів, таких як стандарти європейських систем трубопроводів (наприклад, німецькі стандарти DN) та стандарти американських систем трубопроводів (наприклад, стандарти системи трубопроводів ANSI). Ці стандарти забезпечують якість та взаємозамінність фланців.
Підсумовувати, Охоплений фланець не тільки має переваги стійкості до корозії та стійкості до зносу, але також відіграє важливу роль у зв'язку та герметизації трубопроводів.
Різниця між фланцем для обшивки та фланцем шва
Основна відмінність фланця фланця для обшивки та фланця накладки зварювання - це їх виробничий процес та призначення застосування.
- Процес виробництва :
- Фланець : Цей фланець виготовляється за допомогою технології накладки Weld, це, шар сплаву з корозійною стійкістю (наприклад, Inconel 625) зварений на металевій поверхні матриці. Цей процес часто використовується для поліпшення резистентності до корозії та стійкості до зносу фланців у суворих умовах.
- Фланець шва накладки : Цей фланець також виготовляється за допомогою технології зварювання, Але його основна мета-утворити корозійний або твердий поверхневий шар на трубах та інших металевих деталях. Цей процес може бути застосований до різних матеріалів та методів обробки поверхні.
- Мета застосування :
- Обшивка фланг : в основному використовується в випадках, коли потрібна висока корозійна стійкість, наприклад, морська інженерія, хімічне обладнання, д. Цей фланець забезпечує довгостроковий захист, утворюючи антикорозійний сплавний шар на поверхні фланця.
- Фланець шва накладки : Окрім корозійної стійкості, Він також може бути використаний для поліпшення механічних властивостей та стійкості до зносу фланців. Цей процес широко використовується в нафтогазовій промисловості для забезпечення довгострокової безпеки та надійності трубопроводів та обладнання.
Підсумовуючи, І фланець фланця для обшивки, і фланець зварного шва виробляються за допомогою технології покриття зварювання, Але фланець облицювання зосереджується більше на захисті корозії, в той час як фланець із накладання зварювання більше зосереджується на всебічному поліпшенні продуктивності.
Конкретний процес технології обшивки зварювання
Конкретний процес технології обшивки зварювання:
- Підготовка поверхні : Перший, Очистіть і обробляйте поверхню підкладки для видалення масла, іржаві та старі покриття для того, щоб поверхня була рівною і без домішок. Цей крок має вирішальне значення для якості подальшого зварювання.
- Вибір матеріалу : Виберіть відповідний покрив матеріал відповідно до вимог щодо продуктивності та умов експлуатації підкладки. Поширені покриваючі матеріали включають нержавіючу сталь, Нікельні сплави, сплави на основі кобальту, д. Ці матеріали мають хорошу стійкість до корозії та стійкість до зносу.
- Налаштування параметрів зварювання : Встановіть відповідні параметри зварювання відповідно до вибраного матеріалу та способу зварювання. Загальні методи зварювання включають дугове зварювання (наприклад, ММА), Захисне зварювання газу (Така міг / tha), Зварювання плазмової дуги (наприклад, PTA), д.
- Програми покриття :
- Дугове зварювання : Використовуйте дугу як джерело тепла, щоб розплавити покрив матеріал і осадити його на поверхні підкладки. Загальні методи зварювання дуги включають ручне зварювання металевої дуги (ММА), Заблонене дугове зварювання (Пила), д.
- Зварювання на захист газу : Використовуйте інертний газ (такі як аргон або гелій) Для захисту зони зварювання від окислення. Загальні методи захисту від газового захисту включають зварювання дуги газового металу (Ганчір), Газовий вольфрамовий дуговий зварювання (Gtaw), д.
- Зварювання плазмової дуги : Використовує незаймані вольфрамові електроди та зовнішнє подача газу, підходить для зварювальних процесів з високою енергією та низьким введенням тепла.
- Контроль процесів зварювання :
- Розігріти : Розігрійте підкладку перед зварюванням, щоб зменшити ризик зварювання стресу та тріщин.
- Швидкість зварювання та струм : Відрегулюйте швидкість зварювання та струм за характеристиками матеріалів та методом зварювання, щоб забезпечити рівномірність та якість покриваючого шару.
- Охолодження : Після завершення зварювання, Відповідна обробка охолодження проводиться відповідно до матеріальних характеристик для поліпшення твердості та стійкості.
- Огляд якості :
- Огляд зовнішності : Використовуйте візуальний огляд або УЗД для перевірки поверхневих дефектів шару кришки, такі як пори, тріщина, д.
- Тест на твердість : Твердість шару покриття оцінюється за допомогою тестів на твердість, щоб переконатися, що він відповідає вимогам проектування.
- Аналіз хімічного складу : Використовуйте спектрометр Spark Source Світло (Аес) або рентгенівський флуоресцентний спектрометр (XRF) Для аналізу хімічного складу шару покриву, щоб забезпечити відповідність вимогам проектування.
- Аналіз мікроструктури : Мікроструктуру накладення аналізували за допомогою скануючої електронної мікроскопії (ВООЗ) і трансмісійна електронна мікроскопія (ТЕМ) Оцінити його ефективність.
- Подальше лікування : Термічна обробка або інші поверхневі обробки за потребою, наприклад, шліфування, полірування, і т.д., Для поліпшення якості поверхні та терміну служби шару покриття.
Через вищезазначений процес процесу, Технологія шару зварювального покриву може ефективно утворювати покривний шар із специфічними властивостями на поверхні підкладки, тим самим покращуючи резистентність до корозії, Носистка та механічні властивості підкладки та продовження терміну служби.
Матеріальні характеристики та сценарії застосування корозійного стійкого сплаву (Крем)
Корозійне стійкий шар сплаву (Крем) - це метал або сплав, призначений для протистояння корозії в певному середовищі. CRA підвищує його резистентність. Поширені матеріали CRA включають нержавіючу сталь, Нікельні сплави, Дуплексна нержавіюча сталь і супер дуплексна нержавіюча сталь.
Властивості матеріалу
- Висока корозійна стійкість : CRA може забезпечити довгостроковий захист від корозії в різних суворих умовах, наприклад, океан, хімічні заводи, нафтохімічна промисловість, д.
- Механічні властивості : CRA зазвичай має хороші механічні властивості, такі як висока міцність, Висока твердість і хороша зносостійкість.
- Економічна ефективність : CRA може значно зменшити матеріальні витрати порівняно з усією нержавіючої сталі, особливо у застосуванні з високою товщиною та розмірними варіаціями.
- Зварювальна продуктивність : Матеріали CRA можна переробляти за допомогою різних методів зварювання, наприклад, зварювання TIG, вибухове зварювання, спільно, д.
- Мікроструктура : CRA зазвичай має одну фазу (Кубічний) або двофазна структура, що допомагає покращити його корозійну стійкість та механічні властивості.
Сценарії застосування
- Нафтогазова промисловість : CRA широко використовується у виробництві нафти та газу, збирання та транспортування, підпілля, свердловина та трубопроводи, особливо при високому температурі та високому тиску, Сульфідні та вуглекислий газ. Наприклад, Інконель 625 і 2507 широко використовуються в свердловинних колонах та виробничих трубах.
- Морська техніка : CRA добре працює в морських умовах і підходить для трубопроводів підводних човнів, Морські платформи та інші морські структури. Наприклад, 316L Нержавіюча сталь та дуплексна нержавіюча сталь мають хорошу стійкість до корозії в морських умовах.
- Хімічна промисловість : CRA використовується в хімічній промисловості для виготовлення труб, контейнери та обладнання, особливо при роботі з кислими розчинами та корозійними хімічними речовинами. Наприклад, Інконель 800 і Hastelloy C-276 широко використовуються в хімічній промисловості.
- Геотермальна система виробництва електроенергії : CRA використовується як сендвіч -матеріал у системах генерації геотермальної електроенергії для поліпшення корозійної стійкості до системи трубопроводу. Наприклад, ІНКУНЕЛЬ 625 добре працює в геотермальних системах.
- Будівництво та інфраструктура : CRA використовується в будівництві та інфраструктурі для виготовлення компонентів, таких як труби, клапани та фланці, особливо в умовах, де потрібні висока корозійна стійкість та механічні властивості.
Міркування щодо вибору матеріалів CRA
- Умови навколишнього середовища : температура, Концентрація хлориду, Частковий тиск вуглекислого газу, наявність або відсутність сірки, PH та інші параметри навколишнього середовища впливатимуть на продуктивність CRA.
- Матеріальна вартість : Вибір матеріалів CRA вимагає міркувань економічної ефективності, особливо у застосуванні з високою товщиною та розмірними варіаціями.
- Механічні властивості : Матеріали CRA повинні мати хороші механічні властивості для задоволення потреб конкретних застосувань.
- Зварювальна продуктивність : Матеріали CRA повинні мати хороші продуктивності зварювання, щоб забезпечити якість та надійність під час переробки.
на закінчення
Корозійне стійкий шар сплаву (Крем) є високопродуктивним матеріалом, який широко використовується в декількох галузях промисловості, особливо в умовах, де потрібні висока корозійна стійкість та механічні властивості. Шляхом раціонального вибору матеріалів CRA та з урахуванням умов навколишнього середовища та економічної ефективності, термін служби та надійність обладнання можуть бути значно покращені.
Порівняння витрат між традиційними фланцями з твердого металу та фланцями зварювального покриву
Порівняння витрат між традиційними фланцями з твердого металу та фланцями зварювального покриття можна проаналізувати з декількох аспектів:
- Матеріальна вартість :
- Традиційні фланці з твердого металу зазвичай використовують такі матеріали, як вуглецева сталь або нержавіюча сталь, і вартість відносно низька. Наприклад, Ціна фланців з вуглецевої сталі становить Rs 176,442 (Про долар 2374.73) в Індії, в той час як ціна фланців з нержавіючої сталі вища.
- Зварювальні кришки фланців вимагає додавання корозійних шарів до субстрату, наприклад, Inconel 625 або інконель 718. Ці матеріали дорогі, Особливо ІНКУНЕЛЬ 625, які є дорогими і недоступними при використанні у великих фланцях.
- Вартість виробництва :
- Виробничий процес традиційних фланців із твердого металу відносно простий, в основному залучення кастингу або кування, і вартість низька.
- Процес виробництва фланців зварювального покриву відносно складний, і потрібні кілька процесів, таких як зварювання дуги та лазерне зварювання, що збільшує виробничі витрати.
- Вартість встановлення :
- Традиційні фланці з твердого металу мають менші витрати на встановлення, оскільки вони прості за структурою та меншими етапами встановлення.
- Вартість встановлення фланців зварювального покриву висока, Особливо, коли потрібно декілька зварювання, Витрати на працю та обладнання значно збільшуються.
- Вартість технічного обслуговування :
- Традиційні фланці з твердих металів мають низькі витрати на обслуговування, оскільки вони прості за структурою, хороша стійкість до корозії та тривалий термін служби.
- Хоча фланець зварного покриву має високу стійкість до корозії, Кришка може зношуватися або падати під час тривалого використання, вимагає регулярного обслуговування та заміни, що збільшує витрати на обслуговування.
- Сценарії застосування :
- Традиційні фланці з твердих металів підходять для середовища середнього та низького тиску та середнього температурного середовища, і є рентабельними.
- Зварені фланці кришки підходять для високої температури, Високий тиск та корозійне середовище. Хоча вони дорогі, Вони мають незамінні переваги в конкретних сценаріях додатків.
Підсумовувати, Традиційні фланці з твердого металу мають переваги матеріалу, Витрати на виробництво та обслуговування та підходять для загальних промислових застосувань; в той час як зварювальні фланці мають високу вартість, вони мають кращу резистентність до корозії в конкретних суворих умовах. Продуктивність та термін служби. Конкретний вибір повинен бути всебічно оцінений на основі фактичних сценаріїв застосування та економіки.
Переваги металургійного композитного процесу у виробництві фланця
Переваги металургійного композитного процесу у виробництві фланця в основному відображаються в наступних аспектах:
- Високе використання матеріалу : Через металургійний композитний процес, Переваги різних матеріалів можна поєднувати, наприклад, поєднання алюмінієвого сплаву та сталі, який не тільки підтримує легкі властивості алюмінієвого сплаву, але також використовує високу міцність та корозійну стійкість сталі. Цей композитний матеріал не тільки покращує швидкість використання матеріалу, але також зменшує виробничі витрати.
- Відмінні механічні властивості : Фланці, зроблені металургійним композитним процесом, мають більш високу міцність і міцність, і може витримати більші сили зсуву та розтягування. Наприклад, Міцність пологів з алюмінієвого сплаву може досягти 2-3 в разі чавунних фланців, і не схильні до іржі, і підходять для використання при високому тиску, Висока температура та корозійне середовище.
- Сильна резистентність до корозії : Щільна оксидна плівка, утворена на поверхні алюмінієвого сплаву, і має хорошу корозійну стійкість. Це особливо важливо для виробництва фланців у хімічній речовині, нафту, Морська та інша галузь.
- Хороша теплопровідність : Теплопровідність алюмінієвого сплаву є 3-5 раз, коли чавун, що дозволяє металургійним композитним фланцям ефективніше проводити тепло у середовищах високої температури, Забезпечення нормальної роботи обладнання та продовження терміну служби.
- Висока ефективність виробництва : Металургійний композитний процес може зменшити споживання матеріалів та підвищити ефективність виробництва, покращуючи розробку цвілі та оптимізуючи виробничий процес. Наприклад, Деякі композитні процеси екструзії можуть заощадити 27.9% одного шматка матеріалу, і масове виробництво може заощадити більше ніж 30% вартості сталі.
- Захист навколишнього середовища та стійкість : Металургійні композитні процеси можуть використовувати сталь і інші вторинні матеріали для зменшення ресурсних відходів та забруднення навколишнього середовища. Наприклад, Після алюмінієвого сплаву AA6351 сталь ковзає при 500 ° C, твердість значно покращується, що дозволяє досягти без тріщин або специфічної твердості поверхні.
- Багатофункціональність та адаптованість : Металургійний композитний процес може виробляти фланці з декількома функціями, наприклад, фланці з високою міцністю, Корозійна стійкість та теплопровідність одночасно, підходить для різних складних умов праці.
Підсумовуючи, Металургійний композитний процес має значні переваги у виробництві фланця, включаючи вдосконалення використання матеріалів, Поліпшення механічних властивостей, Посилення резистентності до корозії, Поліпшення теплопровідності, підвищення ефективності виробництва, Досягнення охорони навколишнього середовища та сталого розвитку, та посилення декількох функціональних та пристосованих. Ці переваги змушують металургійні композитні процеси мають широкий спектр перспектив застосування в сучасній промисловості.
Ви повинні бути увійти в систему щоб залишити коментар.