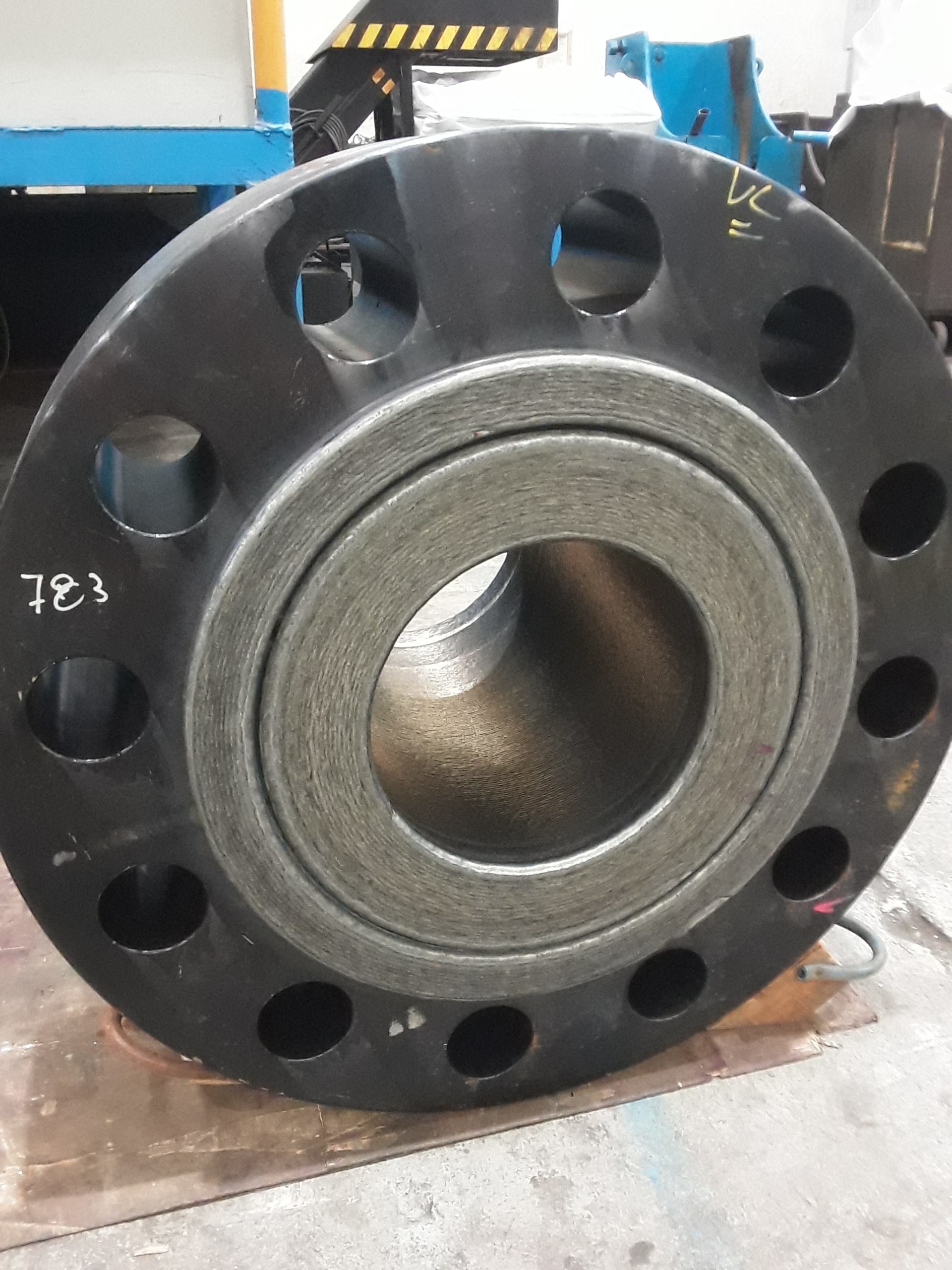
Kaplamalı bayrakların tanımı ve kullanımı
Kaplamalı bayrakların tanımı ve kullanımı aşağıdaki gibidir:
tanım:
Kaplı flanş, flanşın üzerine kaplı kaynak kaplaması olan bir flanş. Bu tedavi genellikle flanşın korozyonunu ve aşınma direncini arttırmak için kullanılır, zorlu ortamlarda kullanılmasına izin vermek.
kullanmak:
- Korozyon Karşıtı Koruma : Kaplı flanş korozyona dayanıklı bir malzeme tabakası ekleyerek korozyonu önler, paslanmaz çelik veya nikel alaşımı gibi, flanşın yüzeyine. Bu, özellikle kimyasal gibi endüstrilerde kullanılan boru hatları ve ekipmanlar için önemlidir., petrol ve gaz.
- Direnç geliştirme aşınma : Girişe dayanıklı bir malzeme katmanı ekleyerek, Kaplı flanş, ekipmanın servis ömrünü uzatabilir ve bakım maliyetlerini azaltabilir.
- Bağlantı ve mühür : Kaplı flanş, boru sistemindeki bir bağlantı bileşenidir ve boruları bağlamak için kullanılır, vanalar, Pompalar ve diğer ekipman. Sistemin güvenli çalışmasını sağlamak için cıvatalar ve rondelalardan sızdırmaz.
- Standartlar ve Spesifikasyonlar : CLAD FLANG, Avrupa Boru Sistemleri Standartları gibi uluslararası ve ulusal standartları takip ediyor (Alman DN standartları gibi) ve Amerikan Boru Sistemleri Standartları (bizim gibi ANSI boru sistemleri standartları). Bu standartlar, flanşların kalitesini ve değiştirilebilirliğini sağlar.
Özetle, Kaplı flanş sadece korozyon direnci ve aşınma direncinin avantajlarına sahip olmakla kalmaz, aynı zamanda boru hattı sistemlerinin bağlantısında ve sızdırmazlığında önemli bir rol oynar.
Kaplama flanşı ve kaynak kaplama flanşı arasındaki fark
Kaplama flanşı ve kaynak kaplama flanşı arasındaki temel fark, üretim süreci ve uygulama amacıdır.
- Üretim süreci :
- Kaplama flanşı : Bu flanş, kaynak kaplama teknolojisi tarafından üretilmiştir, yani, korozyon direnci olan bir alaşım tabakası (Inconel gibi 625) matrisin metal yüzeyine kaynak yapılır. Bu işlem genellikle zorlu ortamlarda korozyon direncini ve flanşın direncini aşındırmak için kullanılır..
- Kaynak kaplama flanşı : Bu flanş ayrıca kaynak örtüsü teknolojisi ile yapılır, Ancak asıl amacı, borular ve diğer metal parçalar üzerinde korozyona dayanıklı veya sert bir yüzey tabakası oluşturmaktır.. Bu işlem çeşitli malzemelere ve yüzey işlem yöntemlerine uygulanabilir.
- Uygulamanın amacı :
- Kaplama flanşı : esas olarak yüksek korozyon direncinin gerekli olduğu durumlarda kullanılır, deniz mühendisliği gibi, kimyasal ekipman, vb. Bu flanş, flanş yüzeyinde korozyon önleyici alaşım tabakası oluşturarak uzun süreli koruma sağlar..
- Kaynak kaplama flanşı : Korozyon direncine ek olarak, Mekanik özellikleri iyileştirmek ve flanşların aşınması için de kullanılabilir.. Bu işlem, petrol ve gaz endüstrisinde, boru hatlarının ve ekipmanların uzun vadeli güvenliğini ve güvenilirliğini sağlamak için yaygın olarak kullanılmaktadır..
Özetle, Hem kaplama flanşı hem de kaynak kaplama flanşı kaynak kapsama teknolojisi ile üretilir, Ancak kaplama flanşı daha çok korozyon korumasına odaklanır, Kaynak kaplama flanşı daha fazla kapsamlı performans geliştirmeye odaklanırken.
Kaynak kaplama kaplama teknolojisinin belirli işlem akışı
Kaynak kaplama kaplama teknolojisinin spesifik işlem akışı aşağıdaki gibidir.:
- Yüzey hazırlığı : Birinci, Yağı çıkarmak için substratın yüzeyini temizleyin ve işleyin, Yüzeyin düz ve safsızlık içermemesini sağlamak için pas ve eski kaplamalar. Bu adım, sonraki kaynağın kalitesi için çok önemlidir.
- Malzeme seçimi : Alt tabakanın performans gereksinimlerine ve çalışma koşullarına göre uygun kaplama malzemesini seçin. Yaygın kaplama malzemeleri paslanmaz çelik içerir, nikel bazlı alaşımlar, Kobalt bazlı alaşımlar, vb. Bu malzemeler iyi korozyon direncine ve aşınma direncine sahiptir.
- Kaynak parametre ayarları : Seçilen malzeme ve kaynak yöntemine göre uygun kaynak parametrelerini ayarlayın. Ortak kaynak yöntemleri ARC kaynağını içerir (MMA gibi), gaz koruyucu kaynağı (Böyle mig / tha), plazma ark kaynağı (PTA gibi), vb.
- Kapsam uygulamaları :
- Ark kaynağı : Kaplama malzemesini eritmek ve substratın yüzeyine yatırmak için bir ısı kaynağı olarak bir ark kullanın. Ortak ark kaynak yöntemleri manuel metal ark kaynağını içerir (MMA), batık ark kaynağı (TESTERE), vb.
- Gaz Koruma Kaynağı : İnert bir gaz kullanın (argon veya helyum gibi) Kaynak alanını oksidasyondan korumak için. Yaygın gaz koruyucu kaynak yöntemleri, gaz metal ark kaynağını içerir (Çiğnemek), gaz tungsten ark kaynağı (GTAW), vb.
- Plazma ark kaynağı : Tüketilmeyen tungsten elektrotları ve harici gaz tedarikini kullanır, Yüksek enerjili ve düşük ısı girişine sahip kaynak işlemleri için uygun.
- Kaynak İşlem Kontrolü :
- Önceden ısıtmak : Kaynak stresi ve çatlak riskini azaltmak için kaynak yapmadan önce substratı önceden ısıtın.
- Kaynak hızı ve akım : Kapak katmanının tekdüzeliğini ve kalitesini sağlamak için kaynak hızını ve akımı malzeme özelliklerine ve kaynak yöntemine göre ayarlayın.
- Soğutma : Kaynak tamamlandıktan sonra, Kapak katmanının sertliğini ve aşınma direncini iyileştirmek için malzeme özelliklerine göre uygun soğutma tedavisi yapılır.
- Kalite denetimi :
- Görünüm muayenesi : Kapak katmanının yüzey kusurlarını kontrol etmek için görsel inceleme veya ultrason kullanın, gözenekler gibi, çatlaklar, vb.
- Sertlik testi : Kapak katmanının sertliği, tasarım gereksinimlerini karşıladığından emin olmak için sertlik testleri ile değerlendirilir.
- Kimyasal bileşim analizi : Kıvılcım Kaynak Işık Emisyon Spektrometresi kullanın (AES) veya X-ışını floresan spektrometresi (XRF) Tasarım gereksinimlerini karşıladığından emin olmak için kapak katmanının kimyasal bileşimini analiz etmek.
- Mikro yapı analizi : Yer paylaşımının mikro yapısı, elektron mikroskopisi taramasıyla analiz edildi (DSÖ) ve transmisyon elektron mikroskopisi (TEM) performansını değerlendirmek için.
- Takip tedavisi : Gerektiğinde ısı işlemi veya diğer yüzey tedavileri, öğütme gibi, parlatma, vb., Kapak katmanının yüzey kalitesini ve servis ömrünü artırmak için.
Yukarıdaki işlem akışı yoluyla, Kaynak kapağı katmanı teknolojisi, substratın yüzeyinde belirli özelliklere sahip bir kapak katmanı etkili bir şekilde oluşturabilir, böylece korozyon direncini iyileştirir, substratın direnci ve mekanik özellikleri ve servis ömrünü uzatan.
Korozyona dayanıklı alaşım tabakasının malzeme özellikleri ve uygulama senaryoları (MKK)
Korozyona dayanıklı alaşım tabakası (MKK) belirli bir ortamda korozyona direnmek için tasarlanmış bir metal veya alaşımdır. CRA, ana metal üzerine bir korozyona dayanıklı alaşım tabakası bırakarak korozyon direncini arttırır. Yaygın MKK malzemeleri paslanmaz çelik içerir, nikel bazlı alaşımlar, dubleks paslanmaz çelik ve süper dubleks paslanmaz çelik.
Malzeme özellikleri
- Yüksek korozyon direnci : MKK, çeşitli zorlu ortamlarda uzun süreli korozyon koruması sağlayabilir, okyanus gibi, kimyasal tesisler, petrokimya endüstrisi, vb.
- Mekanik Özellikler : MKK genellikle yüksek mukavemet gibi iyi mekanik özelliklere sahiptir, Yüksek sertlik ve iyi aşınma direnci.
- Maliyet etkinliği : MKK, tüm paslanmaz çeliğe kıyasla malzeme maliyetlerini önemli ölçüde azaltabilir, özellikle yüksek kalınlık ve boyutsal varyasyonlara sahip uygulamalarda.
- Kaynak performansı : MKK malzemeleri çeşitli kaynak teknikleri ile işlenebilir, Tig kaynağı gibi, patlama kaynağı, ortak, vb.
- Mikroyapı : MKK genellikle tek aşamaya sahiptir (yüz merkezli kübik) veya iki fazlı bir yapı, korozyon direncini ve mekanik özelliklerini geliştirmeye yardımcı olur.
Uygulama senaryoları
- Petrol ve gaz endüstrisi : MKK petrol ve gaz üretiminde yaygın olarak kullanılmaktadır, toplama ve ulaşım, yeraltı, Wellhead ve boru hatları, özellikle yüksek sıcaklık ve yüksek basınçta, hidrojen sülfür ve karbondioksit ortamları. Örneğin, İnkonel 625 ve 2507 Downole sütunlarında ve üretim tüplerinde yaygın olarak kullanılır.
- Deniz Mühendisliği : MKK deniz ortamlarında iyi performans gösterir ve denizaltı boru hatları için uygundur, Deniz platformları ve diğer deniz yapıları. Örneğin, 316L Paslanmaz çelik ve dubleks paslanmaz çelik, deniz ortamlarında iyi korozyon direncine sahiptir.
- Kimya endüstrisi : MKK, kimya endüstrisinde borular üretmek için kullanılır, kaplar ve ekipman, özellikle asidik çözeltiler ve aşındırıcı kimyasallarla uğraşırken. Örneğin, İnkonel 800 ve Hastelloy C-276, kimya endüstrisinde yaygın olarak kullanılmaktadır..
- Jeotermal enerji üretim sistemi : MKK, boru hattı sisteminin korozyon direncini artırmak için jeotermal enerji üretim sistemlerinde bir sandviç malzemesi olarak kullanılır. Örneğin, Inconel 625 jeotermal sistemlerde iyi performans gösterir.
- Bina ve altyapı : CRA, borular gibi bileşenleri üretmek için inşaat ve altyapıda kullanılır, Vanalar ve flanşlar, özellikle yüksek korozyon direnci ve mekanik özelliklerin gerekli olduğu ortamlarda.
MKK Materyalleri Seçme Hususları
- Çevre koşulları : sıcaklık, Klorür iyonu konsantrasyonu, karbondioksit kısmi basınç, kükürt varlığı veya yokluğu, PH ve diğer çevresel parametreler MKK'nın performansını etkileyecektir.
- Maddi maliyet : MKK malzemelerinin seçimi maliyet etkinlik hususları gerektirir, özellikle yüksek kalınlık ve boyutsal varyasyonlara sahip uygulamalarda.
- Mekanik Özellikler : MKK malzemelerinin belirli uygulamaların ihtiyaçlarını karşılamak için iyi mekanik özelliklere sahip olması gerekir.
- Kaynak performansı : MKK malzemelerinin işleme sırasında kalite ve güvenilirliği sağlamak için iyi kaynak performansına sahip olması gerekir.
Sonuç olarak
Korozyona dayanıklı alaşım tabakası (MKK) birden fazla sektörde yaygın olarak kullanılan yüksek performanslı bir malzemedir, özellikle yüksek korozyon direnci ve mekanik özelliklerin gerekli olduğu ortamlarda. Rasyonel olarak CRA materyallerini seçerek ve çevre koşullarını ve maliyet etkinliğini dikkate alarak, Ekipmanın hizmet ömrü ve güvenilirliği önemli ölçüde geliştirilebilir.
Geleneksel katı metal flanşlar ve kaynak kapak flanşları arasında maliyet karşılaştırması
Geleneksel katı metal flanşlar ve kaynak örtüsü flanşları arasındaki maliyet karşılaştırması birçok yönden analiz edilebilir:
- Maddi maliyet :
- Geleneksel katı metal flanşlar genellikle karbon çeliği veya paslanmaz çelik gibi malzemeler kullanır, Ve maliyet nispeten düşük. Örneğin, Karbon çelik flanşlarının fiyatı Rs 176,442 (USD Hakkında 2374.73) Hindistan'da, Paslanmaz çelik flanşların fiyatı daha yüksek olsa da.
- Kaynak kapağı flanşları, substrata korozyona dayanıklı katmanlar eklenmeyi gerektirir, Inconel gibi 625 veya Inconel 718. Bu malzemeler pahalıdır, Özellikle Inconel 625, büyük flanşlarda kullanıldığında pahalı ve uygun olmayan.
- Üretim maliyeti :
- Geleneksel katı metal flanşların üretim süreci nispeten basittir, esas olarak döküm veya dövme dahil, Ve maliyet düşük.
- Kaynak örtüsü flanşlarının üretim süreci nispeten karmaşıktır, ve ark kaynağı ve lazer kaynağı gibi birden fazla işlem gereklidir, bu da üretim maliyetini artırır.
- Kurulum maliyeti :
- Geleneksel katı metal flanşlar daha düşük kurulum maliyetlerine sahiptir, çünkü yapı açısından basittir ve daha az kurulum adımları.
- Kaynak kapağı flanşlarının kurulum maliyeti yüksek, Özellikle birden fazla kaynak gerektiğinde, İş ve ekipman maliyetleri önemli ölçüde arttı.
- Bakım maliyeti :
- Geleneksel katı metal flanşlar, yapıda basit olduğu için düşük bakım maliyetlerine sahiptir, İyi korozyon direnci ve uzun servis ömrü.
- Kaynaklı kapak flanşı yüksek korozyon direncine sahip olmasına rağmen, Kapak uzun süreli kullanım sırasında aşınabilir veya düşebilir, Düzenli bakım ve değiştirme gerektiren, bu da bakım maliyetlerini artırır.
- Uygulama senaryoları :
- Geleneksel katı metal flanşlar, orta ve düşük basınç ve orta sıcaklık ortamları için uygundur, ve uygun maliyetli.
- Kaynaklı kapak flanşları yüksek sıcaklık için uygundur, Yüksek basınç ve aşındırıcı ortamlar. Pahalı olmalarına rağmen, Belirli uygulama senaryolarında yeri doldurulamaz avantajları var.
Özetle, Geleneksel katı metal flanşların malzemede avantajları vardır, imalat ve bakım maliyetleri ve genel endüstriyel uygulamalar için uygundur; Kaynak kapağı flanşlarının yüksek maliyeti vardır, Belirli sert ortamlarda daha iyi korozyon direncine sahipler. Performans ve hizmet ömrü. Özel seçim, gerçek uygulama senaryolarına ve ekonomiye göre kapsamlı bir şekilde değerlendirilmelidir..
Flanş üretiminde metalurjik kompozit sürecin avantajları
Flanş üretiminde metalurjik kompozit sürecin avantajları esas olarak aşağıdaki yönlere yansıtılmaktadır.:
- Yüksek malzeme kullanım : Metalurjik kompozit işlem yoluyla, Farklı malzemelerin avantajları birleştirilebilir, alüminyum alaşım ve çelik kombinasyonu gibi, sadece alüminyum alaşımının hafif özelliklerini korumakla kalmaz, aynı zamanda çeliğin yüksek mukavemeti ve korozyon direncini de kullanır. Bu kompozit malzeme sadece malzemenin kullanım oranını iyileştirmekle kalmaz., aynı zamanda üretim maliyetlerini de azaltır.
- Mükemmel mekanik özellikler : Metalurjik kompozit işlemle yapılan flanşlar daha yüksek mukavemet ve tokluğa sahiptir, ve daha büyük kesme ve gerilme kuvvetlerine dayanabilir. Örneğin, Alüminyum alaşım flanşının gücü ulaşabilir 2-3 dökme demir flanşların zamanları, ve paslanmaya eğilimli değil, ve yüksek basınçta kullanım için uygundur, Yüksek sıcaklık ve aşındırıcı ortamlar.
- Güçlü korozyon direnci : Alüminyum alaşımı yüzeyinde oluşan yoğun oksit film, iç metalin dış ortamla temas etmesini etkili bir şekilde önler, ve iyi korozyon direncine sahiptir. Bu özellikle kimyasalda flanş üretimi için önemlidir, petrol, Deniz ve diğer endüstriler.
- İyi termal iletkenlik : Alüminyum alaşımının termal iletkenliği 3-5 Dökme demirin zamanları, bu da metalurjik kompozit flanşların yüksek sıcaklık ortamlarında ısıyı daha etkili bir şekilde yapmasına izin verir, Ekipmanın normal çalışmasını sağlamak ve hizmet ömrünü uzatma.
- Yüksek Üretim Verimliliği : Metalurjik kompozit işlem, kalıp tasarımını geliştirerek ve üretim sürecini optimize ederek tek parçalı malzeme tüketimini azaltabilir ve üretim verimliliğini artırabilir. Örneğin, Bazı kompozit ekstrüzyon işlemleri tasarruf edebilir 27.9% tek bir malzeme parçası, ve kitle üretimi daha fazla tasarruf edebilir 30% çelik maliyet.
- Çevre Koruma ve Sürdürülebilirlik : Metalurjik kompozit süreçler, kaynak atıklarını ve çevre kirliliğini azaltmak için hurda çelik ve diğer geri dönüştürülmüş malzemeleri kullanabilir. Örneğin, AA6351 alüminyum alaşım hurda çeliği 500 ° C'de dövülür, Sertlik önemli ölçüde geliştirildi, Çatlaksız veya belirli yüzey sertliğinin elde edilmesine izin vermek.
- Çok işlevlilik ve uyarlanabilirlik : Metalurjik kompozit işlem, birden fazla fonksiyona sahip flanşlar üretebilir, yüksek mukavemetli flanşlar gibi, aynı zamanda korozyon direnci ve termal iletkenlik, Çeşitli karmaşık çalışma koşulları için uygun.
Özetle, Metalurjik kompozit işlemin flanş üretiminde önemli avantajları vardır, malzeme kullanımının iyileştirilmesi dahil, Mekanik Özelliklerin Geliştirilmesi, korozyon direncini arttıran, Termal iletkenliğin iyileştirilmesi, Üretim verimliliğini artırmak, Çevre Koruma ve Sürdürülebilir Kalkınma elde etmek, ve çoklu işlevsel ve uyarlanabilir geliştirme. Bu avantajlar, metalurjik kompozit süreçlerin modern endüstride çok çeşitli uygulama beklentilerine sahip olmasını sağlar.
Olmalısın giriş Yorum yazmak için.