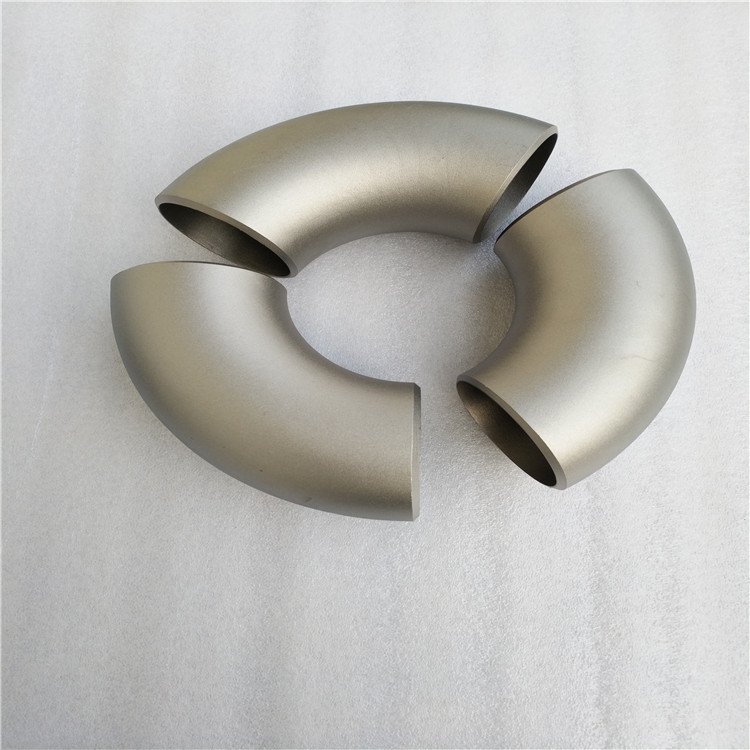
I. Core Content and Scope of ASTM B363 Titanium Alloy Butt-Welding Fittings
The ASTM B363 standard comprehensively governs titanium and titanium alloy butt-welding fittings, primarily for corrosion-resistant and high-temperature service. Key specifications include:
- Material Sources and Processing Requirements
- Raw materials must comply with ASTM standards: plates (B265), bars/billets (B348), forgings (B381), seamless pipes (B861), and welded pipes (B862).
- Manufacturing processes include forging, extrusion, rolling, bending, welding, etc., with strict avoidance of harmful defects.
- Dimensions and Tolerances
- Fittings must conform to ASME B16.9 and MSS SP 43 standards.
- Seamless fittings: ½” to 8″ sizes; wall thickness SCH 5S to SCH 80S.
- Welded fittings: ½” to 16″ sizes; same wall thickness range.
- Examples: Grade 2 seamless 90° elbows (2″ & 4″, SCH 40), concentric reducer (4″×2½″, SCH 40).
- Heat Treatment and Inspection
- Mandatory stress-relieving annealing for optimized mechanical properties.
- Non-destructive testing: 100% PT (penetrant testing) for surfaces, RT (radiographic testing) for welds.
II. Types and Applications of Titanium Butt-Welding Fittings
(A) Common Types
Type | Function & Specifications |
---|---|
Elbows | 45°, 90°, 180° bends; long radius (LR) or short radius (SR) for directional changes. |
Reducers | Concentric/eccentric designs for pipe diameter transitions (e.g., 4″×2½″ SCH 40). |
Tees | Equal/unequal tees, lateral tees for fluid branching. |
Others | Caps, U-bends, lap-joint stub ends, crosses. |
(B) Key Industries
- Chemical & Petrochemical
- Resistant to acids/alkalis in reactors, heat exchangers.
- Aerospace
- Fuel/hydraulic systems: high strength-to-weight ratio reduces structural weight.
- Marine Engineering
- Seawater desalination, subsea pipelines: superior corrosion resistance vs. stainless steel.
- Energy & Power
- High-temperature applications (e.g., nuclear cooling systems), serviceable up to 500°C.
III. Manufacturing Processes & Technical Specifications
(A) Material Processing
- Melting: Vacuum consumable electrode arc melting or electron beam melting for purity.
- Forging: Multi-step upsetting/drawing to refine microstructure.
- Extrusion: Performed at 750–1300°C with glass lubricants; extrusion ratio ~100.
(B) Forming & Welding
- Seamless fittings: Piercing extrusion or cross-rolling.
- Welded fittings: Compliance with ASTM B861/B862; post-weld annealing (450–650°C for 1–5 hours).
IV. Dimensional Standards: ASME B16.9 vs. MSS SP 43
Parameter | ASME B16.9 | MSS SP 43 |
---|---|---|
Scope | Carbon/alloy/stainless steel (NPS ½”–48″) | Thin-wall stainless/nickel alloys (SCH 5S/10S) |
OD Tolerance (NPS≤4″) | ±0.03″ | ±0.03″ (NPS≤4″); +0.06″/-0.03″ (NPS≥5″) |
Pressure Ratings | SCH 10–XXS (full range) | SCH 5S/10S only; short-pattern lap-joints |
V. Impact of Stress-Relieving Annealing
- Mechanical Properties
- Strength reduction: Tensile/yield strength drops 5–10% (e.g., TC18 alloy: 1100 MPa → 950 MPa).
- Ductility improvement: Elongation increases 20–30%; enhanced impact toughness.
- Microstructure
- Above 650°C: Reduced α-phase, increased metastable β-phase.
- Recommended for TA18 alloy: 450–500°C × 3–5 hours.
VI. Product Examples (ASTM B363 Grade 2)
Product | Size | Wall Thickness | Standard |
---|---|---|---|
90° Elbow | 2″ & 4″ | SCH 40 | ASME B16.9 |
Concentric Reducer | 4″×2½″ | SCH 40 | MSS SP 43 |
VII. Quality Control & Testing
- NDT: 100% RT for welds, PT for surface defects.
- Dimensional checks: Laser scanning/CMM for compliance (e.g., elbow angle tolerance ±0.03°–0.75°).
VIII. Industry Trends & Innovations
- Material advancements: High vanadium/molybdenum alloys (e.g., WPT23) for >600°C service.
- Process innovation: Additive manufacturing (3D printing) for complex geometries; lead time reduced to 10–15 days.
This translation provides a technical overview of ASTM B363 titanium alloy fittings, covering standards, manufacturing, applications, and emerging technologies for engineering reference.
You must be logged in to post a comment.