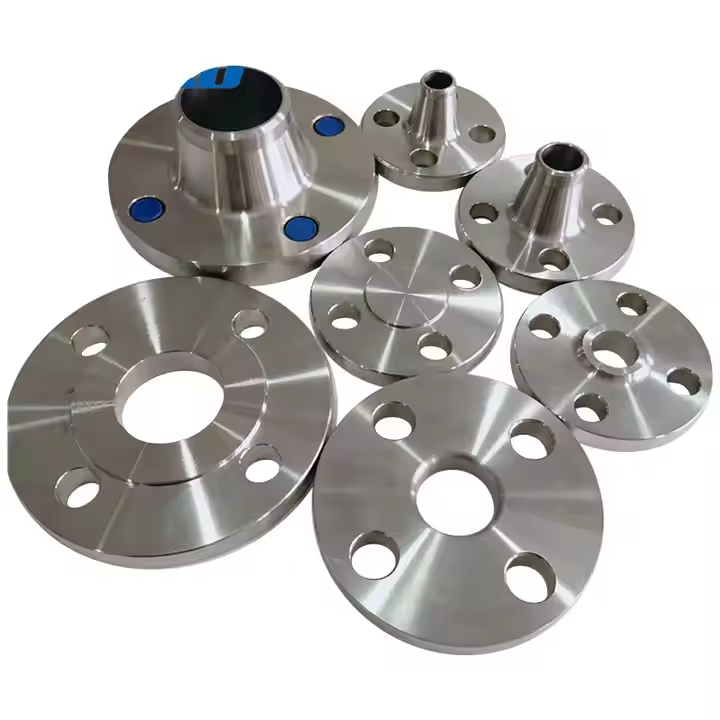
Introduction
As super duplex grades push corrosion limits, emerging alloy chemistries further enhance performance for the most punishing services. F55/UNS S32760 represents one such next-generation duplex steel optimized through small but strategic alloying adjustments. This paper analyzes S32760 flanges by characterizing its microstructure, mechanical properties and corrosion mechanisms to demonstrate advantages over existing alloys for critical applications.
Chemical Composition and Microstructure
S32760 contains 29-31.5% chromium and 4.5-6.5% nickel along with 3.5-5% molybdenum, as per the ASTM A182/ASME SA-182 specification. Similar to super duplex S32750, tungsten levels reach 1.5-3% and nitrogen 0.25-0.35%, promoting delta ferrite formation. However, proprietary additions refine a balanced 60-70% austenite content resulting in higher pitting resistance equivalents (PRE) exceeding 40. This maintains strengths exceeding 130 ksi with 30% minimum elongation, enhancing failure resistance.
Corrosion Performance
Electrochemical evaluations characterize S32760’s superior PRE:
Repassivation rates exceed comparable alloys, rapidly healing breakdowns
Critical pitting temperatures range from 140-160°C, outperforming S32750 by 10°C
Threshold pitting potentials increase by 50mV, mitigating localized corrosion risk
Additionally, the elevated nitrogen content reduces sensitivity to stress corrosion cracking compared to previous super duplex grades.
Fabrication and Inspection
F55 flanges undergo heat treatments and welding as per ASTM A182 to realize optimized properties:
Solution annealing homogenizes phases preventing intermetallic precipitation
Magnetic particle screening and ultra-sonic wall thickness checks qualify integrity
Neutron radiography detects sub-surface imperfections invisible to other techniques
This ensures consistent metallurgy throughout each component meeting demanding offshore pipeline code requirements.
conclusion
With carefully engineered compositions pushing corrosion limits, S32760 duplex flanges deliver significantly improved pitting resistance over existing alloy options. Meticulous fabrication standards coupled with advanced NDT assure as-new condition is sustained throughout design lifetimes. As energy infrastructure scales to ever more extreme environments, F55 will become indispensable for assuring flow assurance and safety.
You must be logged in to post a comment.