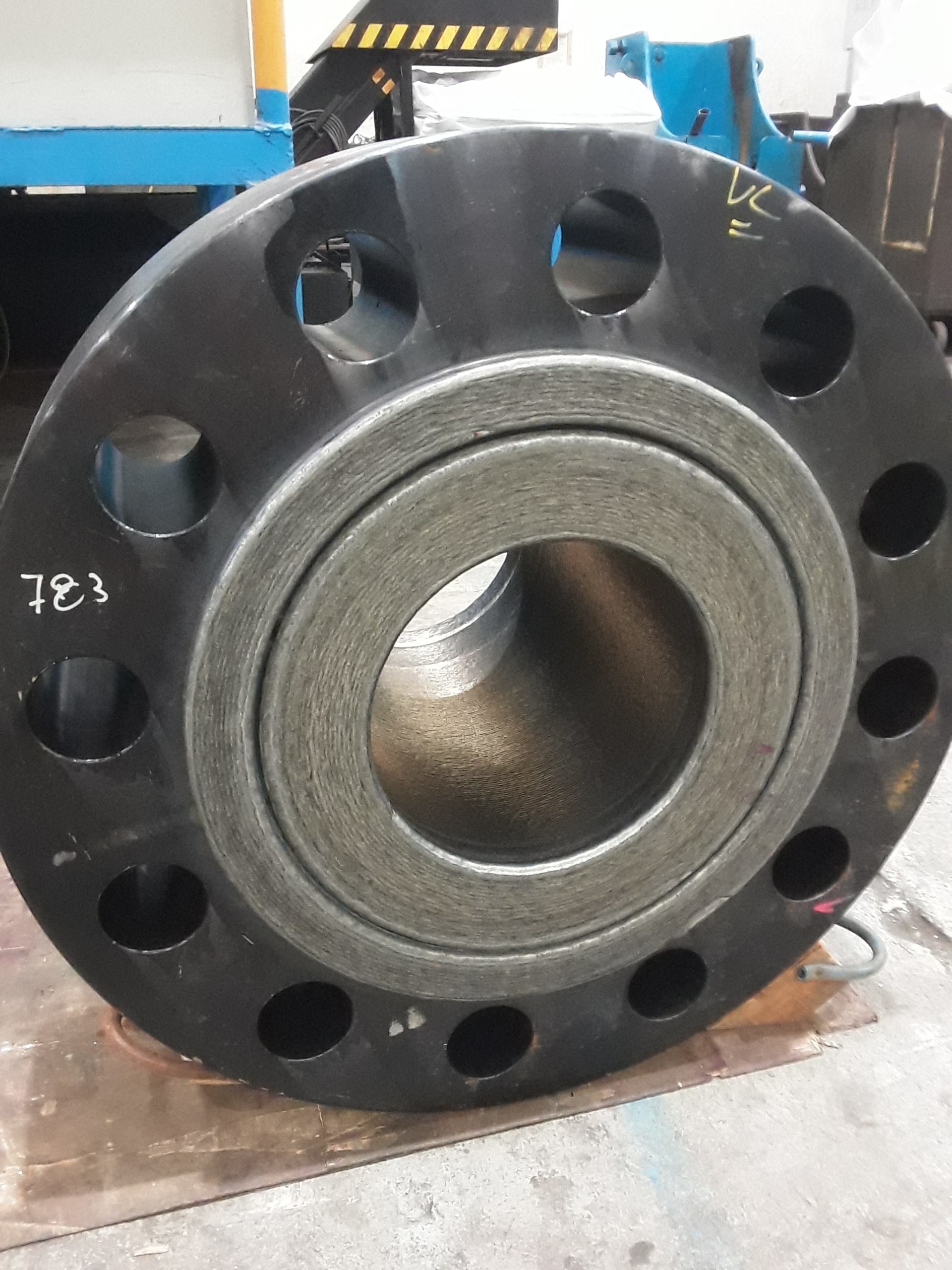
Definición y uso de Flagge Clad
La definición y el uso de la bandera vestida son los siguientes:
definición:
La brida vestida es una brida que es un revestimiento de superposición de soldadura en la brida. Este tratamiento a menudo se usa para mejorar la corrosión y la resistencia al desgaste de la brida, permitiendo que se use en entornos duros.
usar:
- Protección contra la corrosión : La brida vestida previene la corrosión al agregar una capa de material resistente a la corrosión, como acero inoxidable o aleación de níquel, a la superficie de la brida. Esto es especialmente importante para tuberías y equipos utilizados en industrias como químicos, petróleo y gas.
- Mejora de la resistencia al desgaste : Agregando una capa de material resistente al desgaste, La brida vestida puede extender la vida útil del equipo y reducir los costos de mantenimiento.
- Conexión y sello : La brida revestida es un componente de conexión en el sistema de tuberías y se utiliza para conectar tuberías, valvulas, bombas y otros equipos. Se sella a través de pernos y lavadoras para garantizar un funcionamiento seguro del sistema.
- Estándares y especificaciones : Clad Flang sigue estándares internacionales y nacionales, como los estándares de sistemas de tuberías europeas (como los estándares DN alemanes) y estándares de sistemas de tuberías estadounidenses (como los estándares de sistemas de tuberías ANSI de EE. UU.). Estos estándares aseguran la calidad y la intercambiabilidad de las bridas.
Para resumir, La brida vestida no solo tiene las ventajas de la resistencia a la corrosión y la resistencia al desgaste, pero también juega un papel importante en la conexión y el sellado de los sistemas de tuberías.
La diferencia entre la brida de revestimiento y la brida de superposición de soldadura
La principal diferencia entre la brida de revestimiento y la brida de superposición de soldadura es su proceso de fabricación y propósito de la aplicación.
- Proceso de fabricación :
- Brida de revestimiento : Esta brida es fabricada por la tecnología de superposición de Weld, es decir, una capa de aleación con resistencia a la corrosión (como Inconel 625) está soldado en la superficie metálica de la matriz. Este proceso a menudo se usa para mejorar la resistencia a la corrosión y la resistencia al desgaste de las bridas en ambientes hostiles.
- Brida de superposición de soldadura : Esta brida también se realiza a través de la tecnología de cobertura de soldadura, Pero su objetivo principal es formar una capa superficial a prueba de corrosión o dura en tuberías y otras partes metálicas. Este proceso se puede aplicar a una variedad de materiales y métodos de tratamiento de superficie..
- Propósito de la aplicación :
- Brida de revestimiento : principalmente utilizado en ocasiones en las que se requiere alta resistencia a la corrosión, como la ingeniería marina, equipo químico, etcetera. Esta brida proporciona protección a largo plazo al formar una capa de aleación anticorrosión en la superficie de la brida.
- Brida de superposición de soldadura : Además de la resistencia a la corrosión, También se puede utilizar para mejorar las propiedades mecánicas y la resistencia al desgaste de las bridas. Este proceso se utiliza ampliamente en la industria del petróleo y el gas para garantizar la seguridad y confiabilidad a largo plazo de las tuberías y equipos..
En resumen, Tanto la brida de revestimiento como la brida de superposición de soldadura se fabrican a través de la tecnología de cobertura de soldadura, Pero la brida de revestimiento se centra más en la protección de la corrosión, Mientras que la brida de superposición de soldadura se centra más en la mejora integral del rendimiento.
Flujo de proceso específico de la tecnología de revestimiento de superposición de soldadura
El flujo de proceso específico de la tecnología de revestimiento de superposición de soldadura es el siguiente:
- Preparación de la superficie : primero, limpiar y procesar la superficie del sustrato para eliminar el aceite, óxido y recubrimientos viejos para garantizar que la superficie esté plana y libre de impurezas. Este paso es crucial para la calidad de la soldadura posterior..
- Selección de material : Seleccione el material de cobertura apropiado de acuerdo con los requisitos de rendimiento y las condiciones de funcionamiento del sustrato. Los materiales de cobertura común incluyen acero inoxidable, aleaciones a base de níquel, aleaciones a base de cobalto, etcetera. Estos materiales tienen una buena resistencia a la corrosión y resistencia al desgaste..
- Configuración de parámetros de soldadura : Establezca los parámetros de soldadura apropiados de acuerdo con el material seleccionado y el método de soldadura. Los métodos de soldadura comunes incluyen soldadura de arco (como MMA), soldadura protectora de gas (Tal el mig / tha), soldadura por arco de plasma (como PTA), etcetera.
- Aplicaciones de cobertura :
- Soldadura por arco : Use un arco como fuente de calor para derretir el material de cobertura y depositarlo en la superficie del sustrato. Los métodos comunes de soldadura de arco incluyen soldadura manual de arco de metal (MMA), soldadura por arco sumergido (SIERRA), etcetera.
- Soldadura de protección de gas : Usa un gas inerte (como argón o helio) para proteger el área de soldadura de la oxidación. Los métodos de soldadura de protección de gas común incluyen soldadura de arco de metal de gas (Gawn), soldadura de arco de tungsteno de gas (Gtaw), etcetera.
- Soldadura por arco de plasma : Utiliza electrodos de tungsteno no consumidos y suministro de gas externo, Adecuado para procesos de soldadura con alta energía y baja entrada de calor.
- Control de procesos de soldadura :
- Precalentar : Precaliente el sustrato antes de soldar para reducir el riesgo de estrés de soldadura y grietas.
- Velocidad de soldadura y corriente : Ajuste la velocidad y la corriente de soldadura de acuerdo con las características del material y el método de soldadura para garantizar la uniformidad y la calidad de la capa de cobertura.
- Enfriamiento : Después de completar la soldadura, El tratamiento de enfriamiento adecuado se realiza de acuerdo con las características del material para mejorar la dureza y la resistencia al desgaste de la capa de cobertura.
- Inspección de calidad :
- Inspección de apariencia : Use inspección visual o ultrasonido para verificar los defectos de la superficie de la capa de cubierta, como los poros, grietas, etcetera.
- Prueba de dureza : La dureza de la capa de cobertura se evalúa a través de pruebas de dureza para garantizar que cumpla con los requisitos de diseño.
- Análisis de composición química : Use el espectrómetro de emisión de luz de origen de Spark (AES) o espectrómetro de fluorescencia de rayos X (XRF) para analizar la composición química de la capa de cobertura para garantizar que cumpla con los requisitos de diseño.
- Análisis de microestructura : La microestructura de la superposición se analizó mediante microscopía electrónica de barrido (OMS) y microscopía electrónica de transmisión (TEM) para evaluar su rendimiento.
- Tratamiento de seguimiento : Tratamiento térmico u otros tratamientos superficiales según sea necesario, como la molienda, pulido, etcétera, Para mejorar la calidad de la superficie y la vida útil de la capa de cobertura.
A través del flujo de proceso anterior, La tecnología de capa de cubierta de soldadura puede formar efectivamente una capa de cobertura con propiedades específicas en la superficie del sustrato, mejorando así la resistencia a la corrosión, Resistencia al desgaste y propiedades mecánicas del sustrato y extendiendo su vida útil.
Características del material y escenarios de aplicación de la capa de aleación resistente a la corrosión (CRA)
Capa de aleación resistente a la corrosión (CRA) es un metal o aleación diseñada para resistir la corrosión en un entorno específico. CRA mejora su resistencia a la corrosión al depositar una capa de aleación resistente a la corrosión en el metal base. Los materiales de CRA comunes incluyen acero inoxidable, aleaciones a base de níquel, acero inoxidable dúplex y acero inoxidable súper dúplex.
Propiedades de los materiales
- Alta resistencia a la corrosión : CRA puede proporcionar protección contra la corrosión a largo plazo en una variedad de entornos duros, como el océano, plantas quimicas, industria petroquímica, etcetera.
- Propiedades mecánicas : CRA generalmente tiene buenas propiedades mecánicas, como alta resistencia, Alta dureza y buena resistencia al desgaste.
- Rentabilidad : CRA puede reducir significativamente los costos del material en comparación con todo el acero inoxidable, especialmente en aplicaciones con alto espesor y variaciones dimensionales.
- Rendimiento de soldadura : Los materiales de CRA se pueden procesar a través de una variedad de técnicas de soldadura, como la soldadura de TIG, soldadura de explosión, co-rodar, etcetera.
- Microestructura : CRA generalmente tiene una sola fase (cúbico centrado en la cara) o una estructura bifásica, que ayuda a mejorar su resistencia a la corrosión y propiedades mecánicas.
Escenarios de aplicación
- Industria de petróleo y gas : CRA se usa ampliamente en la producción de petróleo y gas., Colección y transporte, subterráneo, cabezal y tuberías, especialmente en alta temperatura y alta presión, ambientes de sulfuro de hidrógeno y dióxido de carbono. Por ejemplo, Inconel 625 y 2507 se usan ampliamente en columnas de fondo de pozo y tubos de producción..
- Ingeniería Marina : CRA funciona bien en entornos marinos y es adecuado para tuberías submarinas, plataformas marinas y otras estructuras marinas. Por ejemplo, 316L acero inoxidable y acero inoxidable dúplex tienen una buena resistencia a la corrosión en ambientes marinos.
- Industria química : CRA se utiliza en la industria química para fabricar tuberías, contenedores y equipos, especialmente cuando se trata de soluciones ácidas y productos químicos corrosivos. Por ejemplo, Inconel 800 y Hastelloy C-276 se utilizan ampliamente en la industria química.
- Sistema de generación de energía geotérmica : CRA se usa como material sándwich en sistemas de generación de energía geotérmica para mejorar la resistencia a la corrosión del sistema de tuberías. Por ejemplo, el inconel 625 funciona bien en los sistemas geotérmicos.
- Edificio e infraestructura : CRA se utiliza en construcción e infraestructura para fabricar componentes como tuberías, válvulas y bridas, especialmente en entornos donde se requieren alta resistencia a la corrosión y propiedades mecánicas.
Consideraciones para elegir materiales CRA
- Condición ambiental : temperatura, concentración de iones de cloruro, Presión parcial de dióxido de carbono, presencia o ausencia de azufre, El pH y otros parámetros ambientales afectarán el rendimiento de CRA.
- Costo de material : La elección de los materiales CRA requiere consideraciones de rentabilidad, especialmente en aplicaciones con alto espesor y variaciones dimensionales.
- Propiedades mecánicas : Los materiales de CRA deben tener buenas propiedades mecánicas para satisfacer las necesidades de aplicaciones específicas.
- Rendimiento de soldadura : Los materiales de CRA deben tener un buen rendimiento de soldadura para garantizar la calidad y la confiabilidad durante el procesamiento.
en conclusión
Capa de aleación resistente a la corrosión (CRA) es un material de alto rendimiento que se usa ampliamente en múltiples industrias, especialmente en entornos donde se requieren alta resistencia a la corrosión y propiedades mecánicas. Seleccionando racionalmente los materiales de CRA y teniendo en cuenta las condiciones ambientales y la rentabilidad, La vida útil y la confiabilidad del equipo pueden mejorarse significativamente.
Comparación de costos entre bridas de metal sólido tradicional y bridas de cubierta de soldadura
La comparación de costos entre las bridas de metal sólido tradicional y las bridas de la cubierta de soldadura se puede analizar a partir de múltiples aspectos:
- Costo de material :
- Las bridas de metal sólido tradicionales generalmente usan materiales como acero al carbono o acero inoxidable, y el costo es relativamente bajo. Por ejemplo, El precio de las bridas de acero al carbono es RS 176,442 (Acerca de USD 2374.73) en la India, mientras que el precio de las bridas de acero inoxidable es más alto.
- Bridas de cubierta de soldadura requiere agregar capas resistentes a la corrosión al sustrato, como Inconel 625 o Inconel 718. Estos materiales son caros, Especialmente el Inconel 625, que son caros e inasequibles cuando se usan en bridas grandes.
- Costo de fabricación :
- El proceso de fabricación de las bridas de metal sólido tradicional es relativamente simple, principalmente involucrando el lanzamiento o la forja, y el costo es bajo.
- El proceso de fabricación de las bridas de la cubierta de soldadura es relativamente complicado, y se requieren múltiples procesos, como la soldadura de arco y la soldadura por láser, que aumenta el costo de fabricación.
- Costo de instalación :
- Las bridas de metal sólido tradicionales tienen costos de instalación más bajos porque tienen una estructura simple y menos pasos de instalación.
- El costo de instalación de las bridas de la cubierta de soldadura es alto, especialmente cuando se requiere soldadura múltiple, Los costos de mano de obra y equipos aumentan significativamente.
- Costo de mantenimiento :
- Las bridas de metal sólido tradicionales tienen bajos costos de mantenimiento porque son simples en estructura, buena resistencia a la corrosión y larga vida útil.
- Aunque la brida de la cubierta soldada tiene alta resistencia a la corrosión, la cubierta puede desgastarse o caer durante el uso a largo plazo, Requerir mantenimiento y reemplazo regulares, que aumenta los costos de mantenimiento.
- Escenarios de aplicación :
- Las bridas de metal sólido tradicionales son adecuadas para ambientes de temperatura media y baja y baja, y son rentables.
- Las bridas de cubierta soldadas son adecuadas para alta temperatura, ambientes de alta presión y corrosivos. Aunque son costosos, Tienen ventajas insustituibles en escenarios de aplicación específicos.
Para resumir, Las bridas de metal sólido tradicionales tienen ventajas en el material, Costos de fabricación y mantenimiento y son adecuados para aplicaciones industriales generales; mientras que las bridas de la cubierta de soldadura tienen un alto costo, Tienen una mejor resistencia a la corrosión en entornos hostiles específicos. Rendimiento y vida útil. La selección específica debe evaluarse de manera integral en función de los escenarios de aplicación y la economía reales.
Ventajas del proceso compuesto metalúrgico en la fabricación de bridas
Las ventajas del proceso compuesto metalúrgico en la fabricación de bridas se reflejan principalmente en los siguientes aspectos:
- Alta utilización de materiales : A través del proceso compuesto metalúrgico, Las ventajas de los diferentes materiales se pueden combinar, como la combinación de aleación de aluminio y acero, que no solo mantiene las propiedades livianas de la aleación de aluminio, pero también utiliza la alta resistencia y la resistencia a la corrosión del acero. Este material compuesto no solo mejora la tasa de utilización del material, pero también reduce los costos de producción.
- Excelentes propiedades mecánicas : Las bridas hechas por el proceso compuesto metalúrgico tienen mayor resistencia y dureza, y puede soportar mayores fuerzas de corte y tracción. Por ejemplo, La resistencia de las partas de la brida de aleación de aluminio puede alcanzar 2-3 veces la de las bridas de hierro fundido, y no son propensos a la óxido, y son adecuados para su uso en alta presión, ambientes de alta temperatura y corrosivo.
- Fuerte resistencia a la corrosión : La película de óxido denso formada en la superficie de la aleación de aluminio evita efectivamente que el metal interno contacte al entorno externo, y tiene buena resistencia a la corrosión. Esto es particularmente importante para la fabricación de bridas en productos químicos, petróleo, marinas y otras industrias.
- Buena conductividad térmica : La conductividad térmica de la aleación de aluminio es 3-5 veces la de hierro fundido, que permite que las bridas compuestas metalúrgicas realicen el calor de manera más efectiva en ambientes de alta temperatura, Asegurar el funcionamiento normal del equipo y extender la vida útil.
- Alta eficiencia de producción : El proceso compuesto metalúrgico puede reducir el consumo de material de una sola pieza y mejorar la eficiencia de producción al mejorar el diseño de moho y la optimización del proceso de producción.. Por ejemplo, Algunos procesos de extrusión compuesta pueden ahorrar 27.9% de una sola pieza de material, y la producción en masa puede ahorrar más de 30% del costo de acero.
- Protección del medio ambiente y sostenibilidad : Los procesos compuestos metalúrgicos pueden utilizar el acero de chatarra y otros materiales reciclados para reducir los desechos de recursos y la contaminación ambiental. Por ejemplo, Después de AA6351, el acero de la aleación de aluminio se forja a 500 ° C, la dureza se mejora significativamente, Permitir que se logre la dureza de la superficie sin grietas o específica.
- Multifuncionalidad y adaptabilidad : El proceso compuesto metalúrgico puede producir bridas con múltiples funciones, tales como bridas con alta fuerza, Resistencia a la corrosión y conductividad térmica al mismo tiempo, Adecuado para una variedad de condiciones de trabajo complejas.
En resumen, El proceso compuesto metalúrgico tiene ventajas significativas en la fabricación de bridas, incluida la mejora de la utilización del material, Mejora de las propiedades mecánicas, Mejora de la resistencia a la corrosión, Mejora de la conductividad térmica, Mejora de la eficiencia de producción, Lograr la protección del medio ambiente y el desarrollo sostenible, y mejorar múltiples funcionales y adaptables. Estas ventajas hacen que los procesos compuestos metalúrgicos tienen una amplia gama de perspectivas de aplicaciones en la industria moderna.
Debes ser iniciado sesión Para publicar un comentario.