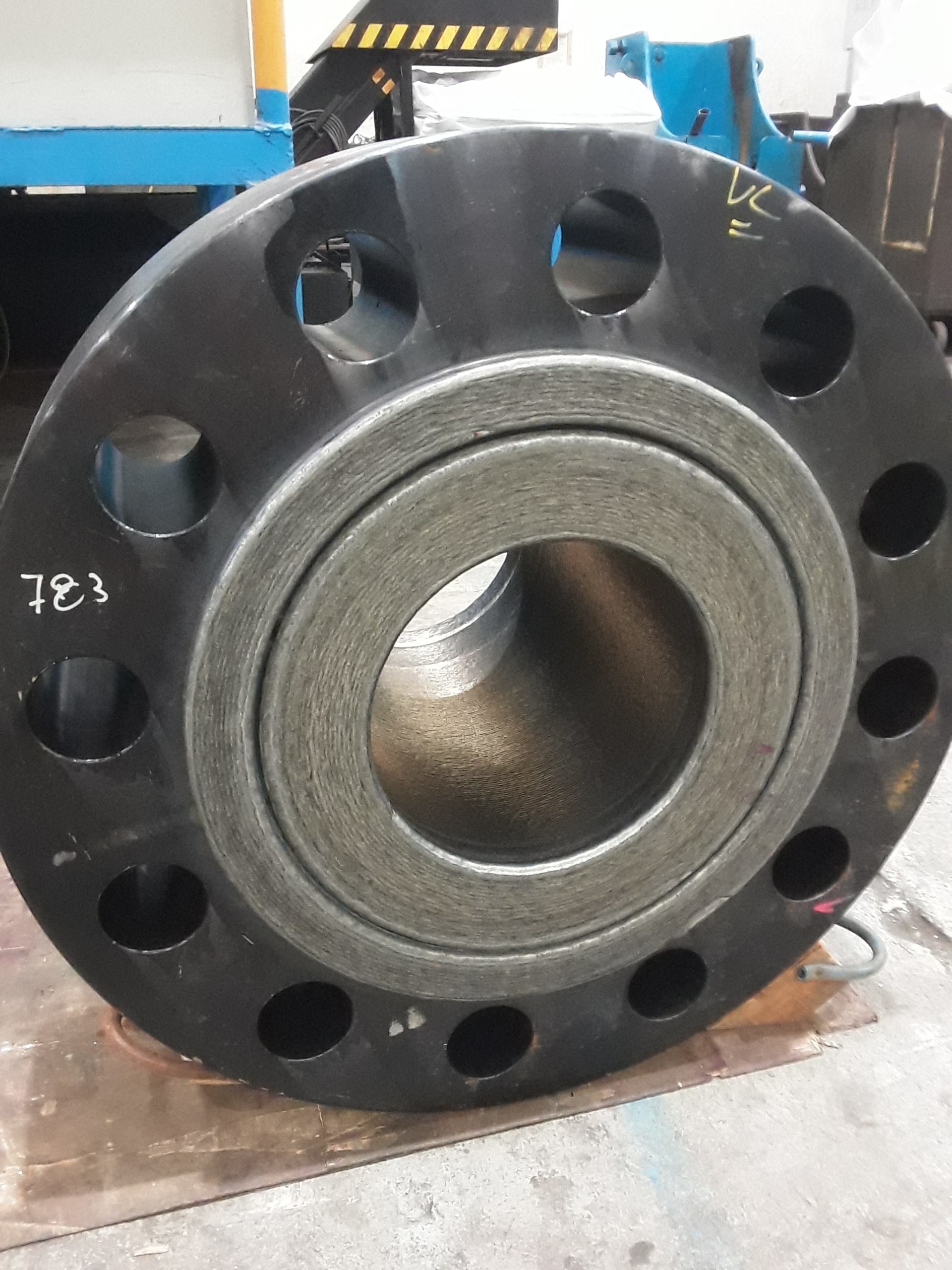
Definition und Verwendung von gekleideter Flagge
Die Definition und Verwendung von verkleidetem Flagge sind wie folgt:
Definition:
Clad Flansch ist ein Flansch. Diese Behandlung wird häufig verwendet, um die Korrosion und den Verschleißfestigkeit des Flansches zu verbessern, zulassen, dass es in harten Umgebungen verwendet wird.
verwenden:
- Antikorrosionsschutz : Der gekleidete Flansch verhindert Korrosion, indem eine Schicht von korrosionsbeständigen Materialien hinzugefügt wird, wie Edelstahl oder Nickellegierung, auf die Oberfläche des Flansches. Dies ist besonders wichtig für Pipelines und Geräte, die in Branchen wie Chemikalie verwendet werden, Öl und Gas.
- Verstärkung der Resistenz : Durch Hinzufügen einer Schicht mit Verschleißmaterial, Clad Flansch kann die Lebensdauer der Ausrüstung verlängern und die Wartungskosten senken.
- Anschluss und Siegel : Der verkleidete Flansch ist eine Verbindungskomponente im Rohrleitungssystem und wird zum Verbinden von Rohren verwendet, Ventile, Pumpen und andere Geräte. Es versiegelt Schrauben und Unterlegscheiben, um einen sicheren Betrieb des Systems zu gewährleisten.
- Normen und Spezifikationen : Clad Flang folgt internationalen und nationalen Standards wie europäischen Rohrleitungssystemen Standards (wie deutsche DN -Standards) und amerikanische Rohrleitungssysteme Standards (wie US -ANSI -Rohrleitungssysteme Standards). Diese Standards gewährleisten die Qualität und Austauschbarkeit der Flansche.
Um zusammenzufassen, Der gekleidete Flansch hat nicht nur die Vorteile von Korrosionsbeständigkeit und Verschleißfestigkeit, spielt aber auch eine wichtige Rolle bei der Verbindung und Versiegelung von Pipeline -Systemen.
Der Unterschied zwischen dem Flansch und dem Schweißgussflansch
Der Hauptunterschied zwischen dem Flansch- und Schweißüberzug -Flansch ist der Herstellungsprozess und der Anwendungszweck.
- Herstellungsprozess :
- KLADDING FLANGE : Dieser Flansch wird mit der Schweißüberzug -Technologie hergestellt, das ist, Eine Legierungsschicht mit Korrosionsbeständigkeit (wie Inconel 625) ist auf der Metalloberfläche der Matrix geschweißt. Dieser Prozess wird häufig verwendet, um die Korrosionsbeständigkeit und den Verschleißfestigkeit von Flanschen in harten Umgebungen zu verbessern.
- Schweißgussflansch : Dieser Flansch wird auch durch Schweißbedeckungstechnologie hergestellt, Sein Hauptzweck ist es jedoch, eine korrosionssichere oder harte Oberflächenschicht auf Rohren und anderen Metallteilen zu bilden. Dieser Prozess kann auf eine Vielzahl von Materialien und Oberflächenbehandlungsmethoden angewendet werden.
- Zweck der Anwendung :
- KLADDE FLANG : hauptsächlich in Anlässen, in denen eine hohe Korrosionsbeständigkeit erforderlich ist, wie Marine Engineering, Chemische Ausrüstung, etc.. Dieser Flansch bietet einen langfristigen Schutz, indem er eine Antikorrosionslegierungsschicht auf der Flanschoberfläche bildet.
- Schweißgussflansch : Zusätzlich zu Korrosionsresistenz, Es kann auch verwendet werden, um die mechanischen Eigenschaften und die Verschleißfestigkeit von Flanschen zu verbessern. Dieser Prozess wird in der Öl- und Gasindustrie häufig verwendet, um eine langfristige Sicherheit und Zuverlässigkeit von Pipelines und Geräten zu gewährleisten.
Zusammenfassend, Sowohl der Flansch- als auch der Schweißüberzug Flansch werden durch Schweißabdeckungstechnologie hergestellt, Aber der Flansch mit dem Verkleidungsflansch konzentriert sich mehr auf den Korrosionsschutz, Während Weld Overlay Flansch mehr auf umfassende Leistungsverbesserungen konzentriert.
Spezifischer Prozessfluss der Schweißverlagerungstechnologie
Der spezifische Prozessfluss der Schweißüberzug -Verkleidungstechnologie ist wie folgt:
- Oberflächenvorbereitung : Zuerst, Reinigen und verarbeiten Sie die Oberfläche des Substrats, um Öl zu entfernen, Rost und alte Beschichtungen, um sicherzustellen, dass die Oberfläche flach und frei von Unreinheiten ist. Dieser Schritt ist entscheidend für die Qualität des nachfolgenden Schweißens.
- Materialauswahl : Wählen Sie das entsprechende Abdeckmaterial gemäß den Leistungsanforderungen und Betriebsbedingungen des Substrats aus. Gemeinsame Deckmaterialien umfassen Edelstahl, Nickelbasierte Legierungen, Kobaltbasierte Legierungen, etc.. Diese Materialien weisen eine gute Korrosionsbeständigkeit und den Verschleißfestigkeit auf.
- Schweißparametereinstellungen : Stellen Sie geeignete Schweißparameter gemäß der ausgewählten Material- und Schweißmethode ein. Gemeinsame Schweißmethoden umfassen Lichtbogenschweißen (wie MMA), Gasschutzschweißen (So die mig / tha), Plasma -Lichtbogenschweißen (wie PTA), etc..
- Deckungsanwendungen :
- Lichtbogenschweißen : Verwenden Sie einen Bogen als Wärmequelle, um das Abdeckmaterial zu schmelzen und auf der Oberfläche des Substrats abzulehnen. Gemeinsame Lichtbogenschweißmethoden enthalten manuelles Metallbogenschweißen (MMA), untergetauchtes Lichtbogenschweißen (GESEHEN), etc..
- Gasschutzschweißen : Verwenden Sie ein inerter Gas (wie Argon oder Helium) Um den Schweißbereich vor Oxidation zu schützen. Häufige Gasschutzschweißmethoden umfassen Gas Metall -Lichtbogenschweißen (Gawn), Bogenschweißen von Gastwolfram (Gtaw), etc..
- Plasma -Lichtbogenschweißen : Verwendet nicht kontrollierbare Wolfram-Elektroden und externe Gasversorgung, Geeignet für Schweißverfahren mit hoher Energie- und niedriger Wärmeeingabe.
- Schweißprozesskontrolle :
- Vorheizen : Heizen Sie das Substrat vor dem Schweißen vor, um das Risiko eines Schweißs und der Risse zu verringern.
- Schweißgeschwindigkeit und Strom : Passen Sie die Schweißgeschwindigkeit und den Strom nach Materialeigenschaften und Schweißverfahren an, um eine Gleichmäßigkeit und Qualität der Abdeckschicht zu gewährleisten.
- Kühlung : Nach Abschluss des Schweißens, Eine angemessene Kühlbehandlung erfolgt nach Materialeigenschaften, um die Härte und den Verschleißfestigkeit der Deckschicht zu verbessern.
- Qualitätsinspektion :
- Aussehensprüfung : Verwenden Sie die Sichtprüfung oder Ultraschall, um die Oberflächendefekte der Abdeckschicht zu überprüfen, wie Poren, Risse, etc..
- Härtetest : Die Härte der Deckschicht wird durch Härtetests bewertet, um sicherzustellen, dass sie den Entwurfsanforderungen entspricht.
- Analyse der chemischen Zusammensetzung : Verwenden Sie Spark Source Light Emission Spectrometer (AES) oder Röntgenfluoreszenzspektrometer (RFA) Analyse der chemischen Zusammensetzung der Deckschicht, um sicherzustellen, dass sie den Entwurfsanforderungen entspricht.
- Mikrostrukturanalyse : Die Mikrostruktur des Overlays wurde durch Rasterelektronenmikroskopie analysiert (WHO) und Transmissionselektronenmikroskopie (Tem) Um seine Leistung zu bewerten.
- Follow-up-Behandlung : Wärmebehandlung oder andere Oberflächenbehandlungen bei Bedarf, wie Schleifen, Polieren, etc., Verbesserung der Oberflächenqualität und der Lebensdauer der Deckschicht.
Durch den obigen Prozessfluss, Die Schichtabdeckungsschichttechnologie kann effektiv eine Abdeckschicht mit spezifischen Eigenschaften auf der Oberfläche des Substrats bilden, Dadurch Verbesserung des Korrosionswiderstands, Verschleißfestigkeit und mechanische Eigenschaften des Substrats und die Verlängerung seiner Lebensdauer.
Materialmerkmale und Anwendungsszenarien der korrosionsresistenten Legierungsschicht (CRA)
Korrosionsbeständige Legierungsschicht (CRA) ist eine Metall oder eine Legierung, die der Korrosion in einer bestimmten Umgebung widersteht. CRA verbessert seinen Korrosionsbeständigkeit, indem sie eine Schicht von korrosionsresistenten Legierung auf dem Grundmetall ablegt. Gemeinsame CRA -Materialien umfassen Edelstahl, Nickelbasierte Legierungen, Duplex Edelstahl und Super Duplex Edelstahl.
Materialeigenschaften
- Hohe Korrosionsbeständigkeit : CRA kann einen langfristigen Korrosionsschutz in einer Vielzahl von harten Umgebungen bieten, wie der Ozean, Chemieanlagen, Petrochemische Industrie, etc..
- Mechanische Eigenschaften : CRA hat normalerweise gute mechanische Eigenschaften wie hohe Festigkeit, hohe Härte und gute Verschleißfestigkeit.
- Kosteneffizienz : CRA kann die Materialkosten im Vergleich zu allen Edelstahl erheblich senken, insbesondere in Anwendungen mit hoher Dicke und dimensionaler Variationen.
- Schweißleistung : CRA -Materialien können durch eine Vielzahl von Schweißtechniken verarbeitet werden, wie TIG -Schweißen, Explosionsschweißen, Co-Rolling, etc..
- Mikrostruktur : CRA hat normalerweise eine einzelne Phase (Gesicht zentriertes Kubikum) oder eine zweiphasige Struktur, Dies hilft, seine Korrosionsbeständigkeit und seine mechanischen Eigenschaften zu verbessern.
Anwendungsszenarien
- Öl- und Gasindustrie : CRA wird in der Öl- und Gasproduktion häufig verwendet, Sammlung und Transport, unterirdisch, Wellkopf und Pipelines, vor allem bei hoher Temperatur und hohem Druck, Schwefelwasserstoffsulfid und Kohlendioxidumgebungen. Zum Beispiel, Inconel 625 und 2507 werden in Downhole -Säulen und Produktionsrohre weit verbreitet verwendet.
- Meerestechnik : CRA funktioniert in Meeresumgebungen gut und eignet sich für U -Boot -Pipelines, Meeresplattformen und andere Meeresstrukturen. Zum Beispiel, 316L Edelstahl und Duplex Edelstahl haben eine gute Korrosionsbeständigkeit in Meeresumgebungen.
- Chemische Industrie : CRA wird in der chemischen Industrie verwendet, um Rohre herzustellen, Behälter und Geräte, vor allem im Umgang mit sauren Lösungen und korrosiven Chemikalien. Zum Beispiel, Inconel 800 und Hastelloy C-276 werden in der chemischen Industrie häufig eingesetzt.
- Geothermie Stromerzeugungssystem : CRA wird als Sandwichmaterial in geothermischen Stromerzeugungssystemen verwendet, um den Korrosionswiderstand des Pipeline -Systems zu verbessern. Zum Beispiel, die Inconel 625 Funktioniert gut in geothermischen Systemen.
- Gebäude und Infrastruktur : CRA wird für den Bau und die Infrastruktur verwendet, um Komponenten wie Rohre herzustellen, Ventile und Flansche, insbesondere in Umgebungen, in denen eine hohe Korrosionsbeständigkeit und mechanische Eigenschaften erforderlich sind.
Überlegungen zur Auswahl von CRA -Materialien
- Umweltbedingungen : Temperatur, Chloridionenkonzentration, Kohlendioxid -Partialdruck, Vorhandensein oder Abwesenheit von Schwefel, pH und andere Umweltparameter beeinflussen die Leistung von CRA.
- Materialkosten : Die Wahl der CRA-Materialien erfordert Kosteneffizienz-Überlegungen, insbesondere in Anwendungen mit hoher Dicke und dimensionaler Variationen.
- Mechanische Eigenschaften : CRA -Materialien müssen über gute mechanische Eigenschaften verfügen, um den Anforderungen bestimmter Anwendungen zu erfüllen.
- Schweißleistung : CRA -Materialien müssen über eine gute Schweißleistung verfügen, um Qualität und Zuverlässigkeit während der Verarbeitung zu gewährleisten.
abschließend
Korrosionsbeständige Legierungsschicht (CRA) ist ein Hochleistungsmaterial, das in mehreren Branchen häufig verwendet wird, insbesondere in Umgebungen, in denen eine hohe Korrosionsbeständigkeit und mechanische Eigenschaften erforderlich sind. Durch rationale Auswahl von CRA-Materialien und unter Berücksichtigung der Umgebungsbedingungen und der Kostenwirksamkeit, Die Lebensdauer und Zuverlässigkeit der Ausrüstung können erheblich verbessert werden.
Kostenvergleich zwischen traditionellen massiven Metallflanschen und Schweißabdeckflanschen
Der Kostenvergleich zwischen herkömmlichen massiven Metallflanschen und Schweißabdeckflanschen kann aus mehreren Aspekten analysiert werden:
- Materialkosten :
- Herkömmliche massive Metallflansche verwenden normalerweise Materialien wie Kohlenstoffstahl oder Edelstahl, und die Kosten sind relativ niedrig. Zum Beispiel, Der Preis für Kohlenstoffstahlflansche beträgt Rs 176,442 (Über USD 2374.73) in Indien, Während der Preis für Edelstahlflansche höher ist.
- Schweißabdeckungsflansche müssen korrosionsresistente Schichten zum Substrat hinzufügen, wie Inconel 625 oder Inconel 718. Diese Materialien sind teuer, vor allem die Inconel 625, die teuer und unerschwinglich sind, wenn sie in großen Flanschen verwendet werden.
- Herstellungskosten :
- Der Herstellungsprozess traditioneller fester Metallflansche ist relativ einfach, hauptsächlich mit Casting oder Schmieden, Und die Kosten sind niedrig.
- Der Herstellungsprozess von Schweißabdeckungsflanschen ist relativ kompliziert, und mehrere Prozesse wie Lichtbogenschweißen und Laserschweißen sind erforderlich, Dies erhöht die Herstellungskosten.
- Installationskosten :
- Herkömmliche massive Metallflansche haben niedrigere Installationskosten, da sie einfach in der Struktur und weniger Installationsschritten sind.
- Die Installationskosten für Schweißabdeckungsflansche sind hoch, vor allem, wenn mehrere Schweißen erforderlich sind, Arbeits- und Ausrüstungskosten sind erheblich erhöht.
- Wartungskosten :
- Herkömmliche massive Metallflansche haben niedrige Wartungskosten, da sie einfach in der Struktur sind, guter Korrosionswiderstand und langes Lebensdauer.
- Obwohl der Flansch der geschweißten Abdeckung einen hohen Korrosionsbeständigkeit aufweist, Die Abdeckung kann während des langfristigen Gebrauchs abnutzen oder fallen, regelmäßige Wartung und Austausch erfordern, die Wartungskosten erhöht.
- Anwendungsszenarien :
- Herkömmliche massive Metallflansche eignen sich für mittel- und niedrig druck- und mittlere Temperaturumgebungen, und sind kostengünstig.
- Schweißabdeckflansche sind für hohe Temperaturen geeignet, Hochdruck und ätzende Umgebungen. Obwohl sie teuer sind, Sie haben unersetzliche Vorteile in bestimmten Anwendungsszenarien.
Um zusammenzufassen, Traditionelle massive Metallflansche haben Vorteile im Material, Herstellungs- und Wartungskosten und eignen sich für allgemeine industrielle Anwendungen; Während Schweißabdeckflansche hohe Kosten haben, Sie haben eine bessere Korrosionsresistenz in bestimmten harten Umgebungen. Leistung und Lebensdauer. Spezifische Auswahl sollte basierend auf tatsächlichen Anwendungsszenarien und Wirtschaftswissenschaften umfassend bewertet werden.
Vorteile des metallurgischen Verbundprozesses in der Flanschherstellung
Die Vorteile des metallurgischen Verbundprozesses in der Flanschherstellung spiegeln sich hauptsächlich in den folgenden Aspekten wider:
- Hohe Materialnutzung : Durch metallurgische Zusammengesetzungsprozess, Die Vorteile verschiedener Materialien können kombiniert werden, wie die Kombination aus Aluminiumlegierung und Stahl, die nicht nur die leichten Eigenschaften der Aluminiumlegierung beibehält, verwendet aber auch die hohe Festigkeit und Korrosionsbeständigkeit von Stahl. Dieses Verbundmaterial verbessert nicht nur die Nutzungsrate des Materials, reduziert aber auch die Produktionskosten.
- Ausgezeichnete mechanische Eigenschaften : Flansche durch metallurgischer Verbundprozess haben eine höhere Stärke und Zähigkeit, und kann größere Scher- und Zugkräfte standhalten. Zum Beispiel, Die Stärke der Aluminiumlegierungsflansch -Schmieden kann erreichen 2-3 mal das von Gusseisenflanschen, und sind nicht anfällig für Rost, und eignen sich für den Verwendung von Hochdruck, Hochtemperatur und ätzende Umgebungen.
- Starke Korrosionsbeständigkeit : Der dichte Oxidfilm, der auf der Oberfläche der Aluminiumlegierung gebildet wird, und hat einen guten Korrosionsbeständigkeit. Dies ist besonders wichtig für die Flanschherstellung in Chemikalie, Petroleum, Marine und andere Branchen.
- Gute thermische Leitfähigkeit : Die thermische Leitfähigkeit der Aluminiumlegierung ist 3-5 mal das von Gusseisen, Dadurch können metallurgische Verbundflansche Wärme in Hochtemperaturumgebungen effektiver durchführen, Gewährleistung des normalen Betriebs der Geräte und der Verlängerung der Lebensdauer.
- Hohe Produktionseffizienz : Der metallurgische Verbundprozess kann einen einzelköpfigen Materialverbrauch verringern und die Produktionseffizienz verbessern, indem die Form des Formteils verbessert und der Produktionsprozess optimiert wird. Zum Beispiel, Einige zusammengesetzte Extrusionsprozesse können sparen 27.9% eines einzelnen Stücks Material, und Massenproduktion kann mehr als sparen als 30% von den Stahlkosten.
- Umweltschutz und Nachhaltigkeit : Metallurgische Verbundprozesse können Schrottstahl und andere recycelte Materialien verwenden, um Ressourcenabfälle und Umweltverschmutzung zu reduzieren. Zum Beispiel, Nach dem AA6351 -Aluminiumlegierungschrottstahl wurde bei 500 ° C geschmiedet, Die Härte ist erheblich verbessert, Ermöglichen.
- Multifunktionalität und Anpassungsfähigkeit : Metallurgischer Verbundprozess kann Flansche mit mehreren Funktionen erzeugen, wie Flansche mit hoher Stärke, Korrosionsresistenz und thermische Leitfähigkeit gleichzeitig, Geeignet für eine Vielzahl komplexer Arbeitsbedingungen.
Zusammenfassend, Der metallurgische Verbundprozess hat erhebliche Vorteile bei der Flanschherstellung, einschließlich der Verbesserung der Materialnutzung, Verbesserung der mechanischen Eigenschaften, Verbesserung der Korrosionsresistenz, Verbesserung der thermischen Leitfähigkeit, Verbesserung der Produktionseffizienz, Umweltschutz und nachhaltige Entwicklung erreichen, und Verbesserung mehrerer funktionaler und anpassungsfähig. Diese Vorteile machen metallurgische Verbundprozesse in der modernen Branche eine breite Palette von Anwendungsaussichten auf.
Du musst sein angemeldet um einen Kommentar zu veröffentlichen.