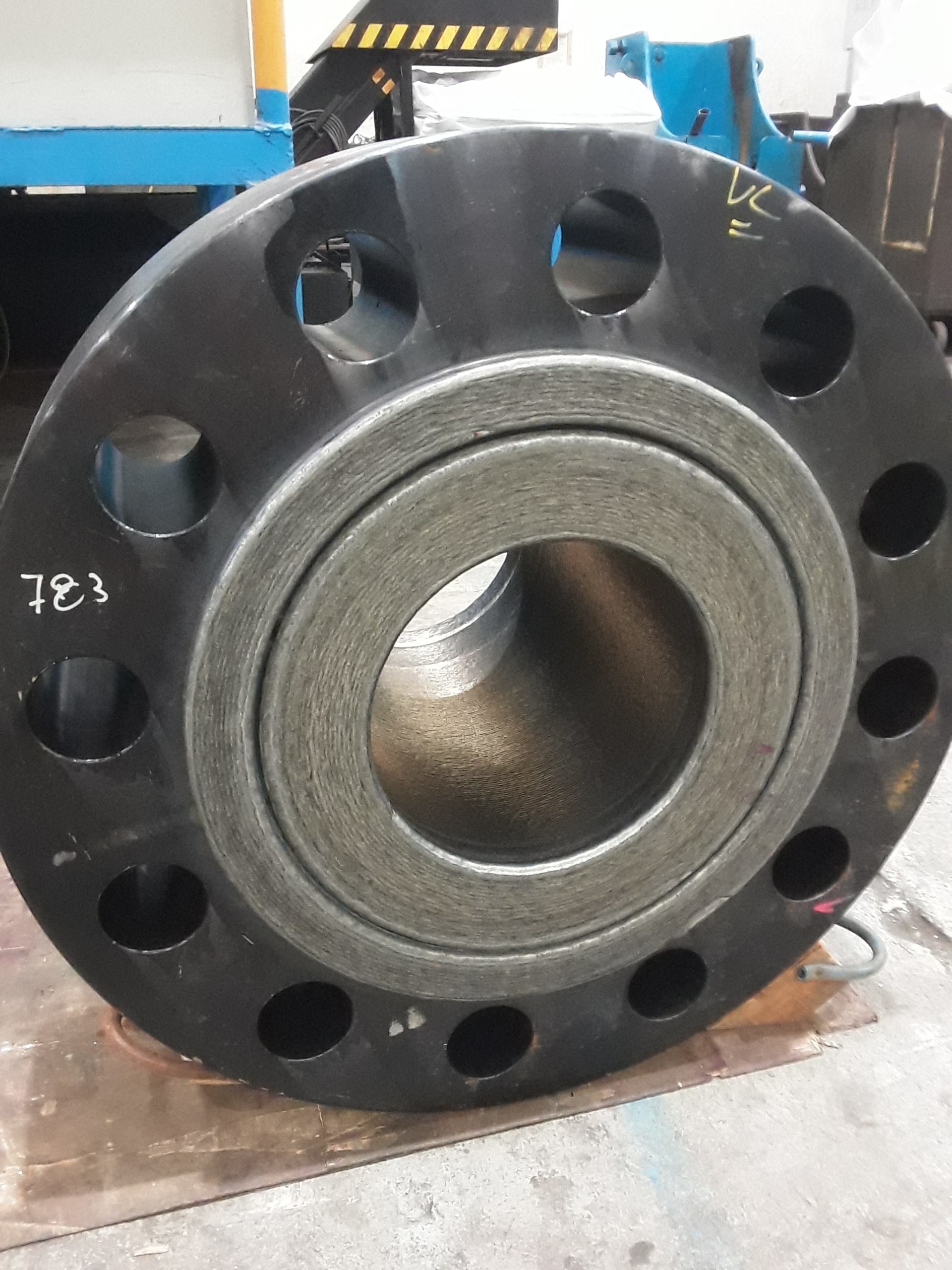
Definition and Use of Clad Flagge
The definition and use of Clad Flagge are as follows:
definition:
Clad Flange is a flange that is weld overlay cladding on the flange. This treatment is often used to improve the corrosion and wear resistance of the flange, allowing it to be used in harsh environments.
use:
- Anti-corrosion protection : Clad Flange prevents corrosion by adding a layer of corrosion-resistant material, such as stainless steel or nickel alloy, to the surface of the flange. This is especially important for pipelines and equipment used in industries such as chemical, oil and gas.
- Wear resistance enhancement : By adding a layer of wear-resistant material, Clad Flange can extend the service life of the equipment and reduce maintenance costs.
- Connection and seal : Clad Flange is a connecting component in the piping system and is used to connect pipes, valves, pumps and other equipment. It seals through bolts and washers to ensure safe operation of the system.
- Standards and Specifications : Clad Flang follows international and national standards such as European piping systems standards (such as German DN standards) and American piping systems standards (such as US ANSI piping systems standards). These standards ensure the quality and interchangeability of the flanges.
To sum up, Clad Flange not only has the advantages of corrosion resistance and wear resistance, but also plays an important role in the connection and sealing of pipeline systems.
The difference between Cladding Flange and Weld Overlay Flange
The main difference between Cladding Flange and Weld Overlay Flange is their manufacturing process and application purpose.
- Manufacturing process :
- Cladding Flange : This flange is manufactured by Weld Overlay technology, that is, a layer of alloy with corrosion resistance (such as Inconel 625) is welded on the metal surface of the matrix. This process is often used to improve the corrosion resistance and wear resistance of flanges in harsh environments.
- Weld Overlay Flange : This flange is also made through welding cover technology, but its main purpose is to form a corrosion-proof or hard surface layer on pipes and other metal parts. This process can be applied to a variety of materials and surface treatment methods.
- Purpose of application :
- Cladding Flang : mainly used in occasions where high corrosion resistance is required, such as marine engineering, chemical equipment, etc. This flange provides long-term protection by forming an anti-corrosion alloy layer on the flange surface.
- Weld Overlay Flange : In addition to corrosion resistance, it can also be used to improve the mechanical properties and wear resistance of flanges. This process is widely used in the oil and gas industry to ensure long-term safety and reliability of pipelines and equipment.
In summary, both Cladding Flange and Weld Overlay Flange are manufactured through welding coverage technology, but Cladding Flange focuses more on corrosion protection, while Weld Overlay Flange focuses more on comprehensive performance improvement.
Specific process flow of Weld Overlay Cladding technology
The specific process flow of Weld Overlay Cladding technology is as follows:
- Surface preparation : First, clean and process the surface of the substrate to remove oil, rust and old coatings to ensure that the surface is flat and free of impurities. This step is crucial to the quality of subsequent welding.
- Material selection : Select the appropriate covering material according to the performance requirements and operating conditions of the substrate. Common covering materials include stainless steel, nickel-based alloys, cobalt-based alloys, etc. These materials have good corrosion resistance and wear resistance.
- Welding parameter settings : Set appropriate welding parameters according to the selected material and welding method. Common welding methods include arc welding (such as MMA), gas protective welding (such as MIG/TIG), plasma arc welding (such as PTA), etc.
- Coverage applications :
- Arc welding : Use an arc as a heat source to melt the covering material and deposit it on the surface of the substrate. Common arc welding methods include manual metal arc welding (MMA), submerged arc welding (SAW), etc.
- Gas protection welding : Use an inert gas (such as argon or helium) to protect the welding area from oxidation. Common gas protective welding methods include gas metal arc welding (GMAW), gas tungsten arc welding (GTAW), etc.
- Plasma arc welding : Uses non-consumable tungsten electrodes and external gas supply, suitable for welding processes with high energy and low heat input.
- Welding process control :
- Preheat : Preheat the substrate before welding to reduce the risk of welding stress and cracks.
- Welding speed and current : Adjust welding speed and current according to material characteristics and welding method to ensure uniformity and quality of the cover layer.
- Cooling : After welding is completed, appropriate cooling treatment is performed according to material characteristics to improve the hardness and wear resistance of the cover layer.
- Quality inspection :
- Appearance inspection : Use visual inspection or ultrasound to check surface defects of the cover layer, such as pores, cracks, etc.
- Hardness Test : The hardness of the cover layer is evaluated through hardness tests to ensure it meets the design requirements.
- Chemical composition analysis : Use spark source light emission spectrometer (AES) or X-ray fluorescence spectrometer (XRF) to analyze the chemical composition of the cover layer to ensure that it meets the design requirements.
- Microstructure Analysis : Microstructure of the overlay was analyzed by scanning electron microscopy (SEM) and transmission electron microscopy (TEM) to evaluate its performance.
- Follow-up treatment : Heat treatment or other surface treatments as needed, such as grinding, polishing, etc., to improve the surface quality and service life of the cover layer.
Through the above process flow, the welding cover layer technology can effectively form a cover layer with specific properties on the surface of the substrate, thereby improving the corrosion resistance, wear resistance and mechanical properties of the substrate and extending its service life.
Material characteristics and application scenarios of corrosion-resistant alloy layer (CRA)
Corrosion-resistant alloy layer (CRA) is a metal or alloy designed to resist corrosion in a specific environment. CRA enhances its corrosion resistance by depositing a layer of corrosion-resistant alloy on the base metal. Common CRA materials include stainless steel, nickel-based alloys, duplex stainless steel and super duplex stainless steel.
Material properties
- High corrosion resistance : CRA can provide long-term corrosion protection in a variety of harsh environments, such as the ocean, chemical plants, petrochemical industry, etc.
- Mechanical properties : CRA usually has good mechanical properties such as high strength, high hardness and good wear resistance.
- Cost-effectiveness : CRA can significantly reduce material costs compared to all stainless steel, especially in applications with high thickness and dimensional variations.
- Welding performance : CRA materials can be processed through a variety of welding techniques, such as TIG welding, explosion welding, co-rolling, etc.
- Microstructure : CRA usually has a single phase (face-centered cubic) or a biphasic structure, which helps improve its corrosion resistance and mechanical properties.
Application scenarios
- Oil and gas industry : CRA is widely used in oil and gas production, collection and transportation, underground, wellhead and pipelines, especially in high temperature and high pressure, hydrogen sulfide and carbon dioxide environments. For example, Inconel 625 and 2507 are widely used in downhole columns and production tubes.
- Marine Engineering : CRA performs well in marine environments and is suitable for submarine pipelines, marine platforms and other marine structures. For example, 316L stainless steel and duplex stainless steel have good corrosion resistance in marine environments.
- Chemical Industry : CRA is used in the chemical industry to manufacture pipes, containers and equipment, especially when dealing with acidic solutions and corrosive chemicals. For example, Inconel 800 and Hastelloy C-276 are widely used in the chemical industry.
- Geothermal Power Generation System : CRA is used as a sandwich material in geothermal power generation systems to improve the corrosion resistance of the pipeline system. For example, the Inconel 625 performs well in geothermal systems.
- Building and Infrastructure : CRA is used in construction and infrastructure to manufacture components such as pipes, valves and flanges, especially in environments where high corrosion resistance and mechanical properties are required.
Considerations for choosing CRA materials
- Environmental conditions : temperature, chloride ion concentration, carbon dioxide partial pressure, presence or absence of sulfur, pH and other environmental parameters will affect the performance of CRA.
- Material Cost : The choice of CRA materials requires cost-effectiveness considerations, especially in applications with high thickness and dimensional variations.
- Mechanical properties : CRA materials need to have good mechanical properties to meet the needs of specific applications.
- Welding performance : CRA materials need to have good welding performance to ensure quality and reliability during processing.
in conclusion
Corrosion-resistant alloy layer (CRA) is a high-performance material that is widely used in multiple industries, especially in environments where high corrosion resistance and mechanical properties are required. By rationally selecting CRA materials and taking into account environmental conditions and cost-effectiveness, the service life and reliability of the equipment can be significantly improved.
Cost comparison between traditional solid metal flanges and welding cover flanges
The cost comparison between traditional solid metal flanges and welding cover flanges can be analyzed from multiple aspects:
- Material Cost :
- Traditional solid metal flanges usually use materials such as carbon steel or stainless steel, and the cost is relatively low. For example, the price of carbon steel flanges is Rs 176,442 (about USD 2374.73) in India, while the price of stainless steel flanges is higher.
- Welding cover flanges requires adding corrosion-resistant layers to the substrate, such as Inconel 625 or Inconel 718. These materials are expensive, especially the Inconel 625, which are expensive and unaffordable when used in large flanges.
- Manufacturing Cost :
- The manufacturing process of traditional solid metal flanges is relatively simple, mainly involving casting or forging, and the cost is low.
- The manufacturing process of welding cover flanges is relatively complicated, and multiple processes such as arc welding and laser welding are required, which increases the manufacturing cost.
- Installation cost :
- Traditional solid metal flanges have lower installation costs because they are simple in structure and fewer installation steps.
- The installation cost of welding cover flanges is high, especially when multiple welding is required, labor and equipment costs are significantly increased.
- Maintenance cost :
- Traditional solid metal flanges have low maintenance costs because they are simple in structure, good corrosion resistance and long service life.
- Although the welded cover flange has high corrosion resistance, the cover may wear or fall off during long-term use, requiring regular maintenance and replacement, which increases maintenance costs.
- Application scenarios :
- Traditional solid metal flanges are suitable for medium and low pressure and medium temperature environments, and are cost-effective.
- Welded cover flanges are suitable for high temperature, high pressure and corrosive environments. Although they are costly, they have irreplaceable advantages in specific application scenarios.
To sum up, traditional solid metal flanges have advantages in material, manufacturing and maintenance costs and are suitable for general industrial applications; while welding cover flanges have high cost, they have better corrosion resistance in specific harsh environments. Performance and service life. Specific selection should be comprehensively evaluated based on actual application scenarios and economics.
Advantages of metallurgical composite process in flange manufacturing
The advantages of metallurgical composite process in flange manufacturing are mainly reflected in the following aspects:
- High material utilization : Through metallurgical composite process, the advantages of different materials can be combined, such as the combination of aluminum alloy and steel, which not only maintains the lightweight properties of aluminum alloy, but also utilizes the high strength and corrosion resistance of steel. This composite material not only improves the utilization rate of the material, but also reduces production costs.
- Excellent mechanical properties : flanges made by metallurgical composite process have higher strength and toughness, and can withstand greater shear and tensile forces. For example, the strength of aluminum alloy flange forgings can reach 2-3 times that of cast iron flanges, and are not prone to rust, and are suitable for use in high pressure, high temperature and corrosive environments.
- Strong corrosion resistance : The dense oxide film formed on the surface of aluminum alloy effectively prevents internal metal from contacting the external environment, and has good corrosion resistance. This is particularly important for flange manufacturing in chemical, petroleum, marine and other industries.
- Good thermal conductivity : The thermal conductivity of aluminum alloy is 3-5 times that of cast iron, which allows metallurgical composite flanges to conduct heat more effectively in high temperature environments, ensuring the normal operation of the equipment and extending service life.
- High production efficiency : Metallurgical composite process can reduce single-piece material consumption and improve production efficiency by improving mold design and optimizing production process. For example, some composite extrusion processes can save 27.9% of a single piece of material, and mass production can save more than 30% of the steel cost.
- Environmental protection and sustainability : Metallurgical composite processes can utilize scrap steel and other recycled materials to reduce resource waste and environmental pollution. For example, after AA6351 aluminum alloy scrap steel is forged at 500°C, the hardness is significantly improved, allowing crack-free or specific surface hardness to be achieved.
- Multifunctionality and adaptability : Metallurgical composite process can produce flanges with multiple functions, such as flanges with high strength, corrosion resistance and thermal conductivity at the same time, suitable for a variety of complex working conditions.
In summary, metallurgical composite process has significant advantages in flange manufacturing, including improving material utilization, improving mechanical properties, enhancing corrosion resistance, improving thermal conductivity, improving production efficiency, achieving environmental protection and sustainable development, and enhancing multiple Functional and adaptable. These advantages make metallurgical composite processes have a wide range of application prospects in modern industry.
You must be logged in to post a comment.