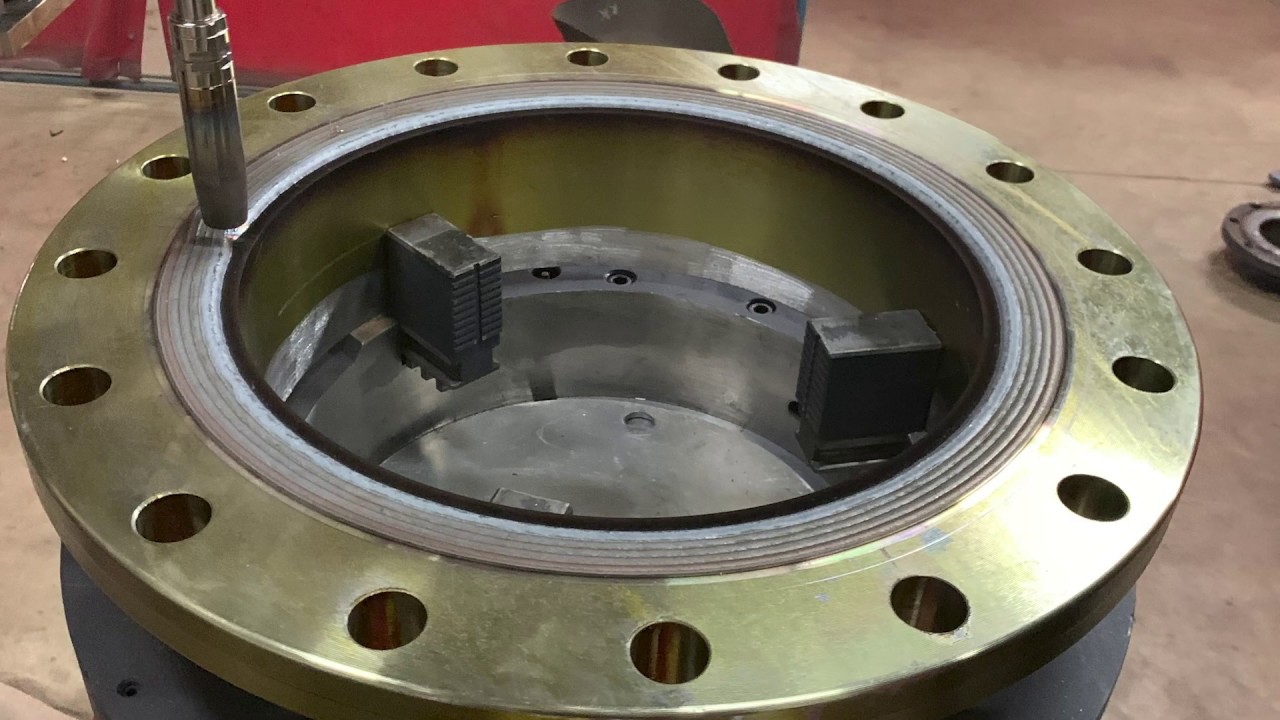
Comprehensive Analysis: Clad Flange/Cladding Flange/Weld Overlay Flange
1. Definition and Core Function
Clad Flange, Cladding Flange, and Weld Overlay Flange are different terms for the same product category. They refer to flanges that utilize weld overlay cladding technology to create a corrosion-resistant alloy (CRA) layer on the surface. The primary purpose is to replace traditional solid metal flanges by combining the strength of a base material (e.g., carbon steel or low-alloy steel) with the corrosion, wear, or high-temperature resistance of the surface cladding.
2. Technical Principles and Process Flow
The weld overlay cladding process involves the following steps:
- Base Material Preparation: Clean and grind the flange surface to remove oxides and contaminants.
- Material Selection: The base material is typically low-cost carbon steel, while the cladding layer uses CRA materials (e.g., Inconel 625, 316L stainless steel).
- Welding Methods:
- GTAW (Gas Tungsten Arc Welding): Suitable for complex geometries and high-precision areas (e.g., flange sealing surfaces).
- GMAW (Gas Metal Arc Welding): High automation for mass production.
- SAW (Submerged Arc Welding): Ideal for large-area uniform cladding.
- Multi-Layer Cladding: Multiple welding passes are applied to control dilution rates (the mixing ratio between the base and cladding materials), ensuring stable chemical composition in the cladding layer.
- Post-Processing: Machining (e.g., turning) to final dimensions and non-destructive testing (e.g., ultrasonic testing) to verify cladding quality.
3. Material Properties and CRA Layer Applications
- CRA Material Properties:
- Inconel 625: High nickel-chromium-molybdenum alloy resistant to H₂S, CO₂, and chloride corrosion, ideal for subsea pipelines and acidic environments.
- Duplex Stainless Steel: Combines austenitic and ferritic structures for resistance to pitting and stress corrosion cracking.
- Monel 400: Nickel-copper alloy resistant to seawater and hydrofluoric acid.
- Applications:
- Offshore Oil & Gas Platforms: Flange sealing surfaces exposed to seawater and acidic fluids.
- Geothermal Power Systems: High-temperature, high-pressure pipelines with corrosive gases.
- Chemical Processing: Reactor flanges requiring resistance to acids or alkalis.
4. Cost Comparison with Traditional Solid CRA Flanges
Comparison Factor | Weld Overlay Flange | Solid CRA Flange |
---|---|---|
Material Cost | 40–60% lower (CRA used only on critical areas; base material is carbon steel) | Extremely high (full CRA material, e.g., Inconel 625) |
Manufacturing Process | Flexible cladding process with customization | Complex forging/casting required |
Maintenance Cost | Local cladding repair avoids full replacement | Full replacement required |
Suitability | Medium to high pressure (Class 150–2500) | May be required for ultra-high-pressure systems |
5. Advantages of Metallurgical Composite Process
- Performance Optimization:
- Corrosion Resistance: CRA layer isolates corrosive media from the base material, extending flange lifespan.
- Strength and Lightweighting: Aluminum-clad flanges are 40% lighter than cast iron with 2–3x higher strength, suitable for aerospace and marine applications.
- Cost Efficiency:
- Material Savings: Composite extrusion reduces raw material use by 27.9%.
- Production Efficiency: Automated welding systems (e.g., Orbital TIG) improve throughput.
- Environmental Adaptability:
- High-Temperature Performance: CRA layers (e.g., Inconel 625) withstand up to 650°C.
- Customization: Cladding thickness (typically 0.25–6 mm) adjustable for specific conditions.
6. Industry Standards and Quality Control
- Standards:
- ASTM A265/A898: Specifications for CRA cladding materials.
- ASME B16.5/B16.47: Flange dimensions and pressure ratings.
- Quality Assurance:
- Dilution Rate Control: Limited to <5% via multi-pass welding to prevent base material contamination.
- Non-Destructive Testing (NDT): Ultrasonic testing for bond integrity; penetrant testing for surface cracks.
7. Case Studies and Applications
- Deep-Sea Oil & Gas Projects: Inconel 625-clad flanges used in X-tree wellheads to resist H₂S and high pressure.
- Coal-Fired Power Plant FGD Systems: 316L stainless steel-clad flanges in flue gas desulfurization equipment, tripling service life over cast iron.
- Nuclear Reactor Piping: Duplex stainless steel-clad flanges in cooling systems for corrosion resistance and radiation stability.
8. Future Trends
- Laser Cladding: Enhances precision and reduces heat-affected zones.
- AI-Driven Welding Robots: Optimize welding paths and parameters using machine learning.
- Green Manufacturing: Recycling CRA waste for cladding to reduce resource consumption.
Summary
Clad Flanges, enabled by weld overlay cladding technology, strike a balance between performance and cost, making them a preferred solution in oil & gas, chemical, and marine industries. Key advantages include customizable material combinations, efficient production, and significant cost savings. As technology evolves, they will further drive industrial equipment toward high performance and sustainability.
You must be logged in to post a comment.