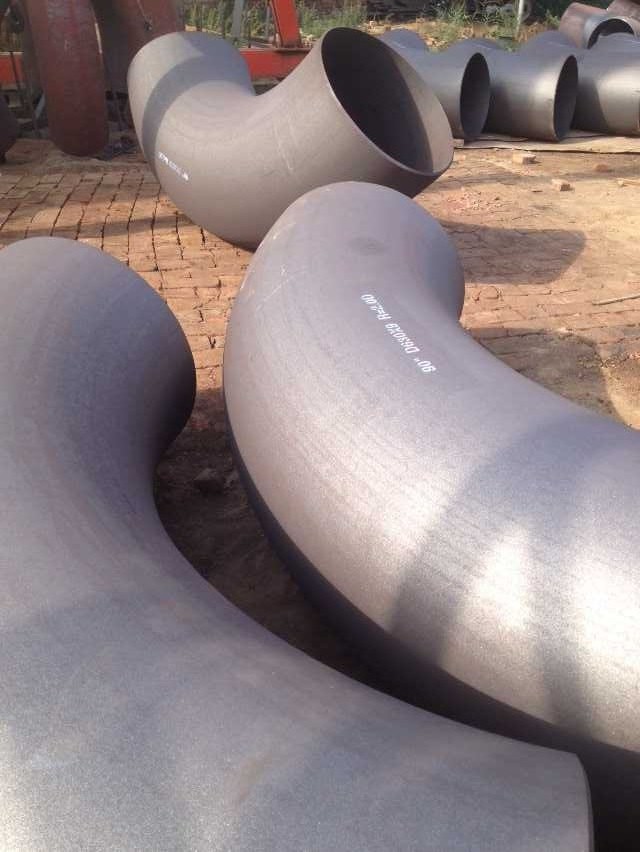
Carbon Steel 2.5D Seamless Pipe Elbow: Specifications, Applications, and Benefits
Introduction
In industrial piping systems, elbows are critical components used to change the direction of flow, typically at angles of 45° or 90°. Among the various types of elbows available, the 2.5D seamless pipe elbow is widely used in applications requiring smooth flow transitions, high strength, and durability. These elbows are made from carbon steel (CS), alloy steel (AS), or stainless steel (SS), and are available in a range of sizes and schedules to meet the specific needs of different industries.
This article provides a comprehensive overview of carbon steel 2.5D seamless pipe elbows, including their specifications, manufacturing process, applications, and benefits. We will also explore the differences between seamless and welded elbows, and provide detailed information on the various schedules (SCH10-SCH80S) and sizes (1/2-24 Inch, DN15-DN600 for seamless elbows and 4-72 Inch, DN150-DN1800 for welded elbows). Additionally, tables will be included to summarize key technical information and specifications.
What is a 2.5D Seamless Pipe Elbow?
A 2.5D seamless pipe elbow is a type of pipe fitting used to change the direction of fluid flow in a piping system. The “2.5D” refers to the radius of the elbow, which is 2.5 times the nominal diameter (D) of the pipe. This larger radius provides a smoother flow transition compared to standard elbows, reducing turbulence and pressure loss.
Key Features of 2.5D Seamless Pipe Elbows:
- Seamless Construction: Seamless elbows are manufactured without any welded joints, providing superior strength and resistance to pressure and corrosion.
- 2.5D Radius: The 2.5D radius ensures a smoother flow transition, reducing pressure drops and minimizing wear and tear on the piping system.
- Material Options: Available in carbon steel (CS), alloy steel (AS), and stainless steel (SS), allowing for use in a wide range of applications and environments.
- Size Range: Seamless elbows are available in sizes ranging from 1/2 inch to 24 inches (DN15-DN600), while welded elbows are available in sizes from 4 inches to 72 inches (DN150-DN1800).
- Pressure Ratings: Available in various schedules, including SCH10, SCH20, SCH40, SCH80, SCH80S, to accommodate different pressure and temperature requirements.
Table 1: Key Characteristics of 2.5D Seamless Pipe Elbows
Characteristic | Description |
---|---|
Elbow Type | Seamless pipe elbow with a 2.5D radius |
Material | Carbon steel (CS), alloy steel (AS), stainless steel (SS) |
Size Range (Seamless) | 1/2 inch to 24 inches (DN15-DN600) |
Size Range (Welded) | 4 inches to 72 inches (DN150-DN1800) |
Pressure Ratings | SCH10, SCH20, SCH40, SCH80, SCH80S |
Applications | Oil & gas, chemical processing, power generation, water treatment, etc. |
Materials Used in 2.5D Seamless Pipe Elbows
The material selection for 2.5D seamless pipe elbows depends on the specific requirements of the application, including factors such as pressure, temperature, and the type of fluid or gas being transported. The most common materials used for these elbows include carbon steel (CS), alloy steel (AS), and stainless steel (SS).
1. Carbon Steel (CS)
Carbon steel is one of the most widely used materials for seamless pipe elbows due to its high strength, durability, and cost-effectiveness. It is suitable for applications where corrosion is not a major concern, such as in oil and gas pipelines, water distribution systems, and general industrial piping.
- Advantages: High strength, cost-effective, easy to fabricate.
- Disadvantages: Susceptible to corrosion in certain environments, such as those containing moisture or corrosive chemicals.
2. Alloy Steel (AS)
Alloy steel contains additional alloying elements, such as chromium, molybdenum, and nickel, which enhance its strength, hardness, and resistance to high temperatures and corrosion. Alloy steel elbows are commonly used in high-temperature and high-pressure applications, such as power generation, petrochemical processing, and refineries.
- Advantages: High strength, excellent resistance to heat and corrosion.
- Disadvantages: More expensive than carbon steel, requires specialized welding techniques.
3. Stainless Steel (SS)
Stainless steel is known for its excellent corrosion resistance, making it ideal for use in corrosive environments, such as chemical processing plants, food and beverage production, and pharmaceutical manufacturing. Stainless steel elbows are available in various grades, including 304, 316, and 321, each offering different levels of corrosion resistance and mechanical properties.
- Advantages: Excellent corrosion resistance, high durability, suitable for hygienic applications.
- Disadvantages: Higher cost compared to carbon steel and alloy steel.
Table 2: Comparison of Materials for 2.5D Seamless Pipe Elbows
Material | Advantages | Disadvantages | Applications |
---|---|---|---|
Carbon Steel (CS) | High strength, cost-effective, easy to fabricate | Susceptible to corrosion in certain environments | Oil & gas, water distribution, general industrial use |
Alloy Steel (AS) | High strength, excellent resistance to heat and corrosion | More expensive, requires specialized welding | Power generation, petrochemical, refineries |
Stainless Steel (SS) | Excellent corrosion resistance, high durability, suitable for hygienic applications | Higher cost compared to carbon and alloy steel | Chemical processing, food & beverage, pharmaceuticals |
Manufacturing Process of 2.5D Seamless Pipe Elbows
The manufacturing process of seamless pipe elbows involves several steps to ensure that the final product meets the required specifications for strength, durability, and dimensional accuracy. The process typically includes the following stages:
1. Raw Material Selection
The first step in manufacturing a seamless pipe elbow is selecting the appropriate raw material, typically a seamless pipe or billet made from carbon steel, alloy steel, or stainless steel. The material is chosen based on the specific requirements of the application, such as pressure, temperature, and corrosion resistance.
2. Cutting
The selected raw material is cut to the required length, depending on the size of the elbow being manufactured. The length of the cut material is determined by the desired radius and angle of the elbow (e.g., 45° or 90°).
3. Heating
The cut pipe or billet is heated in a furnace to a high temperature, typically between 900°C and 1200°C (1650°F to 2200°F), to make the material more malleable and easier to form.
4. Forming
Once the material reaches the desired temperature, it is placed in a forming die, where it is shaped into the required elbow configuration. The forming process may involve several techniques, including hot pushing, mandrel bending, or hydraulic forming, depending on the size and specifications of the elbow.
- Hot Pushing: In this process, the heated pipe is pushed through a die to form the desired elbow shape. The pipe is simultaneously expanded and bent to achieve the required radius and angle.
- Mandrel Bending: A mandrel is inserted into the pipe to prevent it from collapsing during the bending process. The pipe is then bent around a die to form the elbow.
- Hydraulic Forming: Hydraulic pressure is used to expand and bend the pipe into the desired elbow shape.
5. Heat Treatment
After forming, the elbow undergoes heat treatment to relieve internal stresses and improve its mechanical properties. Common heat treatment processes include normalizing, annealing, and quenching and tempering, depending on the material and application requirements.
6. Machining and Finishing
Once the elbow has been heat-treated, it is machined to achieve the required dimensions and surface finish. This may include processes such as trimming, beveling, and polishing. The ends of the elbow are typically beveled to prepare them for welding during installation.
7. Inspection and Testing
The final step in the manufacturing process is inspection and testing to ensure that the elbow meets the required specifications for strength, dimensional accuracy, and surface finish. Common tests include ultrasonic testing, radiographic testing, and hydrostatic testing to check for defects such as cracks, voids, or leaks.
Table 3: Manufacturing Process of 2.5D Seamless Pipe Elbows
Step | Description |
---|---|
Raw Material Selection | Selection of seamless pipe or billet made from carbon steel, alloy steel, or stainless steel |
Cutting | Cutting the raw material to the required length |
Heating | Heating the material to a high temperature to make it malleable |
Forming | Shaping the material into the required elbow configuration using hot pushing, mandrel bending, or hydraulic forming |
Heat Treatment | Relieving internal stresses and improving mechanical properties through normalizing, annealing, or quenching and tempering |
Machining and Finishing | Machining the elbow to achieve the required dimensions and surface finish |
Inspection and Testing | Inspecting and testing the elbow for strength, dimensional accuracy, and surface finish |
Pressure Ratings and Schedules (SCH10-SCH80S)
The pressure rating of a 2.5D seamless pipe elbow is determined by its schedule (SCH), which refers to the wall thickness of the pipe. The schedule affects the elbow’s ability to withstand internal pressure and is an important factor in selecting the appropriate elbow for a given application.
Common Schedules for 2.5D Seamless Pipe Elbows:
- SCH10: Thin-walled, suitable for low-pressure applications.
- SCH20: Slightly thicker than SCH10, used in moderate-pressure applications.
- SCH40: Standard wall thickness, commonly used in a wide range of applications, including water, gas, and steam pipelines.
- SCH80: Thick-walled, suitable for high-pressure applications.
- SCH80S: Similar to SCH80 but with a slightly different wall thickness, often used in stainless steel piping systems.
Table 4: Pressure Ratings and Schedules for 2.5D Seamless Pipe Elbows
Schedule | Wall Thickness (inches) | Pressure Rating (psi) | Applications |
---|---|---|---|
SCH10 | 0.109 – 0.148 | 150 – 300 | Low-pressure applications, such as water distribution and HVAC systems |
SCH20 | 0.147 – 0.216 | 300 – 600 | Moderate-pressure applications, such as gas pipelines and industrial water systems |
SCH40 | 0.154 – 0.337 | 600 – 1500 | Standard applications, including steam, gas, and water pipelines |
SCH80 | 0.218 – 0.500 | 1500 – 3000 | High-pressure applications, such as oil and gas pipelines and chemical processing |
SCH80S | 0.218 – 0.500 | 1500 – 3000 | High-pressure stainless steel piping systems |
Seamless vs. Welded Elbows
When selecting a pipe elbow, it is important to understand the differences between seamless and welded elbows, as each type has its own advantages and disadvantages.
1. Seamless Elbows
Seamless elbows are manufactured from a single piece of material, without any welded joints. This provides superior strength and resistance to pressure, making seamless elbows ideal for high-pressure and high-temperature applications.
- Advantages: No welded joints, higher strength, better resistance to pressure and corrosion.
- Disadvantages: More expensive than welded elbows, limited size range (typically up to 24 inches).
2. Welded Elbows
Welded elbows are made by joining two pieces of material together using welding techniques. While welded elbows are generally less expensive than seamless elbows, they may have lower strength and resistance to pressure due to the presence of welded joints.
- Advantages: Lower cost, available in larger sizes (up to 72 inches).
- Disadvantages: Welded joints may be weaker than seamless construction, potential for corrosion at the weld seam.
Table 5: Comparison of Seamless and Welded Elbows
Type | Advantages | Disadvantages | Applications |
---|---|---|---|
Seamless Elbows | No welded joints, higher strength, better resistance to pressure and corrosion | More expensive, limited size range (up to 24 inches) | High-pressure, high-temperature applications |
Welded Elbows | Lower cost, available in larger sizes (up to 72 inches) | Welded joints may be weaker, potential for corrosion at the weld seam | Low to moderate pressure applications, large-diameter pipelines |
Applications of 2.5D Seamless Pipe Elbows
2.5D seamless pipe elbows are used in a wide range of industries and applications where smooth flow transitions, high strength, and durability are required. Some of the key industries and applications include:
1. Oil and Gas Industry
In the oil and gas industry, seamless pipe elbows are used in pipelines that transport crude oil, natural gas, and refined petroleum products. The high strength and corrosion resistance of carbon steel and alloy steel elbows make them ideal for use in harsh environments, such as offshore platforms and refineries.
2. Chemical Processing
In chemical processing plants, seamless pipe elbows are used to transport corrosive chemicals and high-temperature fluids. Stainless steel elbows are commonly used in these applications due to their excellent corrosion resistance and ability to withstand high temperatures.
3. Power Generation
In power plants, seamless pipe elbows are used in high-pressure steam and water pipelines. Alloy steel elbows are often used in these applications due to their ability to withstand high temperatures and pressures.
4. Water Treatment and Distribution
In water treatment plants and municipal water distribution systems, seamless pipe elbows are used to transport water at various pressure levels. Carbon steel elbows are commonly used in these applications due to their strength and cost-effectiveness.
5. Food and Beverage Industry
In the food and beverage industry, stainless steel seamless pipe elbows are used in hygienic piping systems that transport food-grade liquids, such as milk, juice, and beer. The smooth surface of stainless steel prevents contamination and ensures easy cleaning and sterilization.
Table 6: Common Applications of 2.5D Seamless Pipe Elbows
Industry | Application |
---|---|
Oil & Gas | Pipelines for crude oil, natural gas, and refined petroleum products |
Chemical Processing | Transport of corrosive chemicals and high-temperature fluids |
Power Generation | High-pressure steam and water pipelines |
Water Treatment | Municipal water distribution systems |
Food & Beverage | Hygienic piping systems for food-grade liquids |
Conclusion
Carbon steel 2.5D seamless pipe elbows are essential components in industrial piping systems, offering smooth flow transitions, high strength, and durability. Available in a wide range of sizes and pressure ratings (SCH10-SCH80S), these elbows are suitable for a variety of applications, including oil and gas, chemical processing, power generation, and water treatment. The seamless construction of these elbows ensures superior strength and resistance to pressure and corrosion, making them ideal for use in high-pressure and high-temperature environments.
By understanding the key characteristics, materials, manufacturing process, and applications of 2.5D seamless pipe elbows, engineers and designers can select the most appropriate elbow for their specific needs, ensuring the long-term reliability and efficiency of their piping systems.
FAQ
What is a 2.5D seamless pipe elbow?
A 2.5D seamless pipe elbow is a type of pipe fitting used to change the direction of fluid flow in a piping system. The “2.5D” refers to the radius of the elbow, which is 2.5 times the nominal diameter of the pipe. Seamless elbows are manufactured without any welded joints, providing superior strength and resistance to pressure and corrosion.
What materials are used for 2.5D seamless pipe elbows?
2.5D seamless pipe elbows are commonly made from carbon steel (CS), alloy steel (AS), and stainless steel (SS). The material selection depends on the specific requirements of the application, such as pressure, temperature, and corrosion resistance.
What is the difference between seamless and welded elbows?
Seamless elbows are manufactured from a single piece of material without any welded joints, providing higher strength and resistance to pressure and corrosion. Welded elbows are made by joining two pieces of material together using welding techniques. While welded elbows are generally less expensive, they may have lower strength and resistance to pressure due to the presence of welded joints.
What are the common applications of 2.5D seamless pipe elbows?
2.5D seamless pipe elbows are used in a wide range of industries, including oil and gas, chemical processing, power generation, water treatment, and food and beverage. They are ideal for applications requiring smooth flow transitions, high strength, and durability.
What are the pressure ratings for 2.5D seamless pipe elbows?
The pressure rating of a 2.5D seamless pipe elbow is determined by its schedule (SCH), which refers to the wall thickness of the pipe. Common schedules include SCH10, SCH20, SCH40, SCH80, and SCH80S, with pressure ratings ranging from 150 psi to 3000 psi, depending on the schedule and material.
You must be logged in to post a comment.