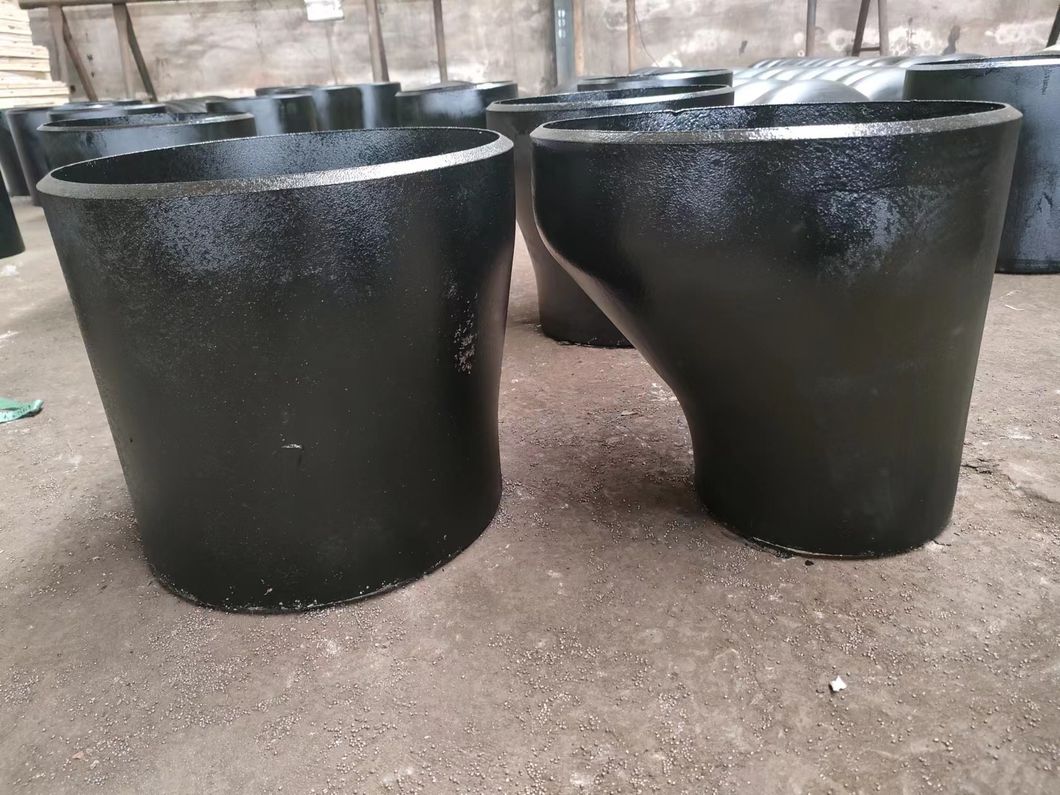
Comprehensive Guide to Buttweld Pipe Reducers: SMLS 1/2″-24″, Welded 4″-72″
Introduction
In industrial piping systems, buttweld pipe reducers play a critical role in connecting pipes of different diameters while maintaining the integrity of the flow. These reducers are essential in systems that require a smooth transition between pipes of varying sizes, ensuring minimal turbulence and pressure drop. The reducers come in two primary types: seamless (SMLS) reducers and welded reducers, with sizes ranging from 1/2 inch to 24 inches for seamless reducers and 4 inches to 72 inches for welded reducers.
This article provides a detailed overview of buttweld pipe reducers, including their specifications, materials, wall thickness options, and applications. We will also explore the differences between seamless and welded reducers, and provide tables summarizing the key technical information. Additionally, this guide will cover the various material standards, such as carbon steel, alloy steel, stainless steel, and low-temperature steel, used in the manufacturing of buttweld pipe reducers.
What is a Buttweld Pipe Reducer?
A buttweld pipe reducer is a type of pipe fitting used to connect two pipes of different diameters. The reducer allows for a smooth transition between the two pipes, reducing the risk of turbulence and pressure loss. Buttweld reducers are typically available in two configurations:
- Concentric Reducers: These reducers have a conical shape and are used when the centerline of both pipes remains the same.
- Eccentric Reducers: These reducers have an off-center design and are used when the pipes need to be aligned along one edge.
Key Features of Buttweld Pipe Reducers:
- Seamless Construction (SMLS): Seamless reducers are manufactured without any welded joints, providing superior strength and resistance to pressure and corrosion.
- Welded Construction: Welded reducers are made by joining two pieces of material together, offering a cost-effective solution for larger sizes.
- Size Range: Seamless reducers are available in sizes from 1/2 inch to 24 inches (DN15-DN600), while welded reducers are available in sizes from 4 inches to 72 inches (DN150-DN1800).
- Wall Thickness: Available in a wide range of wall thicknesses, including SCH10, SCH20, SCH30, STD, SCH40, SCH60, XS, SCH80, SCH100, SCH120, SCH140, SCH160, XXS, and more.
- Maximum Thickness: Buttweld reducers can have a maximum wall thickness of 120mm, depending on the material and size.
Table 1: Key Characteristics of Buttweld Pipe Reducers
Characteristic | Description |
---|---|
Reducer Type | Seamless (SMLS) or welded buttweld pipe reducer |
Material | Carbon steel, alloy steel, stainless steel, low-temperature steel, high-performance steel |
Size Range (Seamless) | 1/2 inch to 24 inches (DN15-DN600) |
Size Range (Welded) | 4 inches to 72 inches (DN150-DN1800) |
Wall Thickness | SCH10, SCH20, SCH30, STD, SCH40, SCH60, XS, SCH80, SCH100, SCH120, SCH140, SCH160, XXS, SCH5S, SCH20S, SCH40S, SCH80S |
Maximum Thickness | 120mm |
Applications | Oil & gas, chemical processing, power generation, water treatment, etc. |
Materials Used in Buttweld Pipe Reducers
The material selection for buttweld pipe reducers depends on the specific requirements of the application, such as pressure, temperature, and the type of fluid or gas being transported. The most common materials used for these reducers include carbon steel, alloy steel, stainless steel, low-temperature steel, and high-performance steel.
1. Carbon Steel (CS)
Carbon steel is one of the most widely used materials for buttweld pipe reducers due to its high strength, durability, and cost-effectiveness. Carbon steel reducers are suitable for applications where corrosion is not a major concern, such as in oil and gas pipelines, water distribution systems, and general industrial piping.
- Common Standards: ASTM/ASME A234 WPB, WPC
- Advantages: High strength, cost-effective, easy to fabricate.
- Disadvantages: Susceptible to corrosion in certain environments, such as those containing moisture or corrosive chemicals.
2. Alloy Steel (AS)
Alloy steel contains additional alloying elements, such as chromium, molybdenum, and nickel, which enhance its strength, hardness, and resistance to high temperatures and corrosion. Alloy steel reducers are commonly used in high-temperature and high-pressure applications, such as power generation, petrochemical processing, and refineries.
- Common Standards: ASTM/ASME A234 WP1, WP12, WP11, WP22, WP5, WP91, WP911
- Advantages: High strength, excellent resistance to heat and corrosion.
- Disadvantages: More expensive than carbon steel, requires specialized welding techniques.
3. Stainless Steel (SS)
Stainless steel is known for its excellent corrosion resistance, making it ideal for use in corrosive environments, such as chemical processing plants, food and beverage production, and pharmaceutical manufacturing. Stainless steel reducers are available in various grades, including 304, 316, and 321, each offering different levels of corrosion resistance and mechanical properties.
- Common Standards: ASTM/ASME A403 WP304, WP304L, WP304H, WP316, WP316L, WP316H, WP321, WP321H, WP347, WP347H
- Advantages: Excellent corrosion resistance, high durability, suitable for hygienic applications.
- Disadvantages: Higher cost compared to carbon steel and alloy steel.
4. Low-Temperature Steel
Low-temperature steel is designed for applications that involve extremely low temperatures, such as cryogenic processing or transportation of liquefied gases. These reducers are made from materials that maintain their toughness and strength at low temperatures.
- Common Standards: ASTM/ASME A402 WPL3, WPL6
- Advantages: Suitable for low-temperature applications, maintains toughness at low temperatures.
- Disadvantages: Limited to specific applications, higher cost than standard carbon steel.
5. High-Performance Steel
High-performance steel is used in applications that require exceptional strength and toughness, such as high-pressure pipelines and offshore platforms. These steels are designed to withstand extreme conditions, including high temperatures, high pressures, and corrosive environments.
- Common Standards: ASTM/ASME A860 WPHY42, WPHY46, WPHY52, WPHY60, WPHY65, WPHY70
- Advantages: Exceptional strength and toughness, suitable for high-pressure applications.
- Disadvantages: Higher cost, requires specialized fabrication techniques.
Table 2: Comparison of Materials for Buttweld Pipe Reducers
Material | Common Standards | Advantages | Disadvantages | Applications |
---|---|---|---|---|
Carbon Steel (CS) | ASTM/ASME A234 WPB, WPC | High strength, cost-effective, easy to fabricate | Susceptible to corrosion in certain environments | Oil & gas, water distribution, general industrial use |
Alloy Steel (AS) | ASTM/ASME A234 WP1, WP12, WP11, WP22, WP5, WP91, WP911 | High strength, excellent resistance to heat and corrosion | More expensive, requires specialized welding | Power generation, petrochemical, refineries |
Stainless Steel (SS) | ASTM/ASME A403 WP304, WP304L, WP316, WP316L, WP321, WP347 | Excellent corrosion resistance, high durability, suitable for hygienic applications | Higher cost compared to carbon and alloy steel | Chemical processing, food & beverage, pharmaceuticals |
Low-Temperature Steel | ASTM/ASME A402 WPL3, WPL6 | Suitable for low-temperature applications, maintains toughness at low temperatures | Limited to specific applications, higher cost than standard carbon steel | Cryogenic processing, liquefied gas transportation |
High-Performance Steel | ASTM/ASME A860 WPHY42, WPHY46, WPHY52, WPHY60, WPHY65, WPHY70 | Exceptional strength and toughness, suitable for high-pressure applications | Higher cost, requires specialized fabrication techniques | High-pressure pipelines, offshore platforms |
Wall Thickness and Schedules for Buttweld Pipe Reducers
The wall thickness of a buttweld pipe reducer is a critical factor in determining its pressure rating and suitability for different applications. The wall thickness is typically specified using schedules (SCH), which refer to the nominal wall thickness of the pipe. The most common schedules for buttweld pipe reducers include SCH10, SCH20, SCH30, STD, SCH40, SCH60, XS, SCH80, SCH100, SCH120, SCH140, SCH160, XXS, and SCH5S, SCH20S, SCH40S, SCH80S for stainless steel applications.
Common Schedules for Buttweld Pipe Reducers:
- SCH10: Thin-walled, suitable for low-pressure applications.
- SCH20: Slightly thicker than SCH10, used in moderate-pressure applications.
- SCH30: Intermediate wall thickness, used in medium-pressure applications.
- STD (Standard): Standard wall thickness, commonly used in a wide range of applications.
- SCH40: Standard wall thickness, suitable for medium to high-pressure applications.
- SCH60: Thicker than SCH40, used in high-pressure applications.
- XS (Extra Strong): Extra thick wall, suitable for high-pressure and high-temperature applications.
- SCH80: Thick-walled, suitable for high-pressure applications.
- SCH100-SCH160: Used in very high-pressure applications.
- XXS (Double Extra Strong): Extremely thick wall, used in the most demanding high-pressure applications.
- SCH5S, SCH20S, SCH40S, SCH80S: Special schedules for stainless steel applications, offering thinner walls for specific applications.
Table 3: Wall Thickness and Schedules for Buttweld Pipe Reducers
Schedule | Wall Thickness (inches) | Pressure Rating (psi) | Applications |
---|---|---|---|
SCH10 | 0.109 – 0.148 | 150 – 300 | Low-pressure applications, such as water distribution and HVAC systems |
SCH20 | 0.147 – 0.216 | 300 – 600 | Moderate-pressure applications, such as gas pipelines and industrial water systems |
SCH30 | 0.216 – 0.250 | 600 – 900 | Medium-pressure applications, such as steam pipelines |
STD | 0.250 – 0.337 | 600 – 1500 | Standard applications, including steam, gas, and water pipelines |
SCH40 | 0.154 – 0.337 | 600 – 1500 | Medium to high-pressure applications |
SCH60 | 0.218 – 0.500 | 1500 – 3000 | High-pressure applications, such as chemical processing and oil pipelines |
XS | 0.337 – 0.500 | 1500 – 3000 | High-pressure and high-temperature applications |
SCH80 | 0.218 – 0.500 | 1500 – 3000 | High-pressure applications, such as oil and gas pipelines and chemical processing |
SCH100-SCH160 | 0.500 – 0.750 | 3000 – 6000 | Very high-pressure applications |
XXS | 0.750 – 1.000 | 6000+ | Extremely high-pressure applications |
SCH5S, SCH20S, SCH40S, SCH80S | 0.109 – 0.500 | 150 – 3000 | Special schedules for stainless steel applications |
Seamless vs. Welded Buttweld Pipe Reducers
When selecting a buttweld pipe reducer, it is important to understand the differences between seamless and welded reducers, as each type has its own advantages and disadvantages.
1. Seamless Buttweld Pipe Reducers
Seamless reducers are manufactured from a single piece of material, without any welded joints. This provides superior strength and resistance to pressure, making seamless reducers ideal for high-pressure and high-temperature applications.
- Advantages: No welded joints, higher strength, better resistance to pressure and corrosion.
- Disadvantages: More expensive than welded reducers, limited size range (typically up to 24 inches).
2. Welded Buttweld Pipe Reducers
Welded reducers are made by joining two pieces of material together using welding techniques. While welded reducers are generally less expensive than seamless reducers, they may have lower strength and resistance to pressure due to the presence of welded joints.
- Advantages: Lower cost, available in larger sizes (up to 72 inches).
- Disadvantages: Welded joints may be weaker than seamless construction, potential for corrosion at the weld seam.
Table 4: Comparison of Seamless and Welded Buttweld Pipe Reducers
Type | Advantages | Disadvantages | Applications |
---|---|---|---|
Seamless Reducers | No welded joints, higher strength, better resistance to pressure and corrosion | More expensive, limited size range (up to 24 inches) | High-pressure, high-temperature applications |
Welded Reducers | Lower cost, available in larger sizes (up to 72 inches) | Welded joints may be weaker, potential for corrosion at the weld seam | Low to moderate pressure applications, large-diameter pipelines |
Applications of Buttweld Pipe Reducers
Buttweld pipe reducers are used in a wide range of industries and applications where smooth flow transitions, high strength, and durability are required. Some of the key industries and applications include:
1. Oil and Gas Industry
In the oil and gas industry, buttweld pipe reducers are used in pipelines that transport crude oil, natural gas, and refined petroleum products. The high strength and corrosion resistance of carbon steel and alloy steel reducers make them ideal for use in harsh environments, such as offshore platforms and refineries.
2. Chemical Processing
In chemical processing plants, buttweld pipe reducers are used to transport corrosive chemicals and high-temperature fluids. Stainless steel reducers are commonly used in these applications due to their excellent corrosion resistance and ability to withstand high temperatures.
3. Power Generation
In power plants, buttweld pipe reducers are used in high-pressure steam and water pipelines. Alloy steel reducers are often used in these applications due to their ability to withstand high temperatures and pressures.
4. Water Treatment and Distribution
In water treatment plants and municipal water distribution systems, buttweld pipe reducers are used to transport water at various pressure levels. Carbon steel reducers are commonly used in these applications due to their strength and cost-effectiveness.
5. Food and Beverage Industry
In the food and beverage industry, stainless steel buttweld pipe reducers are used in hygienic piping systems that transport food-grade liquids, such as milk, juice, and beer. The smooth surface of stainless steel prevents contamination and ensures easy cleaning and sterilization.
Table 5: Common Applications of Buttweld Pipe Reducers
Industry | Application |
---|---|
Oil & Gas | Pipelines for crude oil, natural gas, and refined petroleum products |
Chemical Processing | Transport of corrosive chemicals and high-temperature fluids |
Power Generation | High-pressure steam and water pipelines |
Water Treatment | Municipal water distribution systems |
Food & Beverage | Hygienic piping systems for food-grade liquids |
Conclusion
Buttweld pipe reducers are essential components in industrial piping systems, providing a smooth transition between pipes of different diameters while maintaining the integrity of the flow. Available in a wide range of sizes and wall thicknesses, these reducers are suitable for a variety of applications, including oil and gas, chemical processing, power generation, and water treatment. The seamless construction of these reducers ensures superior strength and resistance to pressure and corrosion, making them ideal for use in high-pressure and high-temperature environments.
By understanding the key characteristics, materials, wall thickness options, and applications of buttweld pipe reducers, engineers and designers can select the most appropriate reducer for their specific needs, ensuring the long-term reliability and efficiency of their piping systems.
FAQ
What is a buttweld pipe reducer?
A buttweld pipe reducer is a type of pipe fitting used to connect two pipes of different diameters. It allows for a smooth transition between the two pipes, reducing the risk of turbulence and pressure loss. Buttweld reducers are available in seamless and welded configurations.
What materials are used for buttweld pipe reducers?
Buttweld pipe reducers are commonly made from carbon steel, alloy steel, stainless steel, low-temperature steel, and high-performance steel. The material selection depends on the specific requirements of the application, such as pressure, temperature, and corrosion resistance.
What is the difference between seamless and welded buttweld reducers?
Seamless reducers are manufactured from a single piece of material without any welded joints, providing higher strength and resistance to pressure and corrosion. Welded reducers are made by joining two pieces of material together using welding techniques. While welded reducers are generally less expensive, they may have lower strength and resistance to pressure due to the presence of welded joints.
What are the common applications of buttweld pipe reducers?
Buttweld pipe reducers are used in a wide range of industries, including oil and gas, chemical processing, power generation, water treatment, and food and beverage. They are ideal for applications requiring smooth flow transitions, high strength, and durability.
You must be logged in to post a comment.