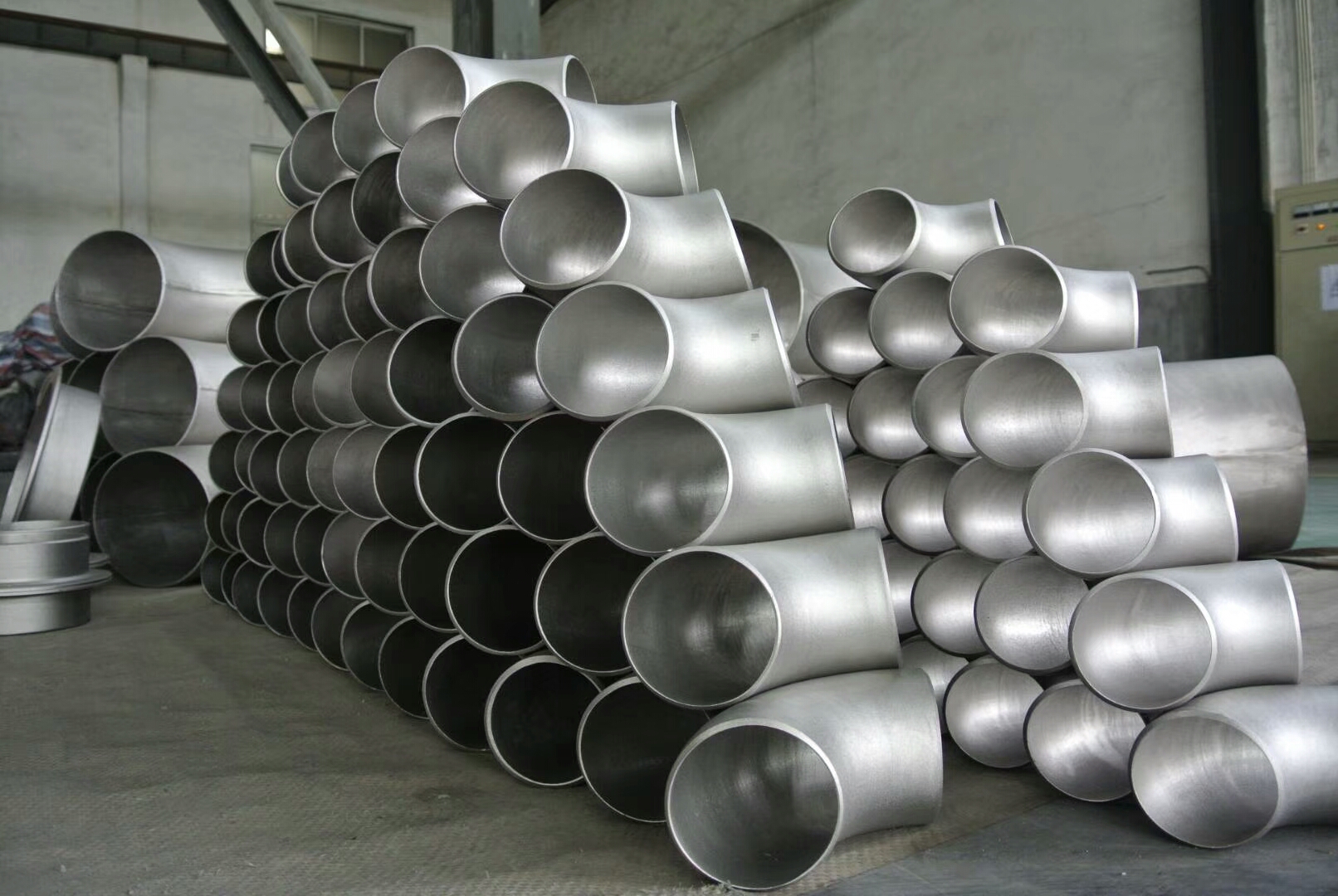
Specific content and scope of application of ASTM B363 standard
The ASTM B363 standard mainly involves seamless and welded pure titanium and titanium alloy welding accessories, suitable for general corrosion resistance and high temperature services. This standard specifies the size, shape and tolerances of titanium and titanium alloy pipe fittings, and requires that these pipe fittings must comply with the provisions of relevant standards such as ASTM B3265, ASTM B3388, ASTM B348, ASTM B381, etc.
Specifically, the ASTM B363 standard covers the following:
- Material requirements : The standard applies to pure titanium and titanium alloy materials, including but not limited to WPT1, WPT2, WPT2W and other levels.
- Size and shape : The standard specifies the dimensions of fittings, such as the DN15-DN600 (NPS 1/2” – 24”), with wall thickness ranging from 1/16 inch to 2 inches.
- Connection methods : including seamless connection and welding connection. Common connection methods include 45° and 90° elbows, 180° back bends, diameter reduction, cap, tee, cross, side tee, U-shaped elbows, overlapping End and so on.
- Quality control : The standard requires 100% X-ray inspection and 100% surface penetration inspection to ensure the quality of the pipe fittings.
- Application field : The standard is applicable to chemical, petroleum, machinery, industry and other fields, especially in applications that require corrosion resistance and high temperature environments.
In addition, the ASTM B363 standard is consistent with other relevant standards such as ASME B16.9, ANSI B16.9, etc., ensuring consistency and interchangeability in the international market.
Common types and application scenarios of titanium alloy fittings
The common types and application scenarios of titanium alloy fittings are as follows:
Common Types
- Titanium elbows :
- Includes 45°, 90° and 180° elbows to change the direction of fluid in the ducting system. These elbows can be manufactured according to ASME B16.9 and ASME B16.11 standards, and are available in different sizes and wall thicknesses.
- Titanium Tees :
- Used to connect the pipe and branch out another pipe. It is divided into two types: concentric and eccentric.
- Titanium reducer connectors :
- It is used to connect pipes of different diameters, and is divided into two types: concentric and eccentric.
- Titanium flanges :
- Including blind flanges, grangs, blind plate flanges, welded flanges, etc., for connecting and sealing of pipeline systems.
- Titanium connectors :
- Used to connect the two pipe ends to ensure continuous flow of fluid.
- Other types :
- Including caps, lap-joint stub ends, U-shaped bends, etc.
Application scenarios
- Aerospace :
- Titanium alloy pipe fittings are widely used in aerospace pipeline systems, such as engines, aircraft systems and missile structural materials, due to their lightweight, high-strength, high temperature resistance and oxidation resistance.
- Chemical Industry :
- It is used in chemical reactors, heat exchangers and acid-base conveying pipes, especially in corrosive environments, titanium alloy pipe fittings show excellent corrosion resistance.
- Marine Engineering :
- In seawater environment, titanium alloy pipe fittings can resist the corrosion of salt water and are suitable for submarine pipelines, marine platforms, and seawater desalination equipment.
- Oil and gas industry :
- It is used in natural gas transportation, oil extraction and other fields, and can withstand harsh working environments with high temperature and high pressure.
- Medical equipment :
- Titanium alloy pipe fittings are also used in medical equipment, such as certain special medical pipes and equipment, due to their good biocompatibility and corrosion resistance.
- Other industrial fields :
- Including power, ship manufacturing, electroplating industry, etc., titanium alloy pipe fittings are widely used for their high strength, corrosion resistance and good mechanical properties.
To sum up, titanium alloy pipe fittings play an important role in many fields with high technical requirements. Their diverse types and wide application scenarios make them an indispensable part of modern industry.
Dimension parameters of ASTM B363 Grade 2 seamless pipe fittings (such as 2″ & 4″ 90° elbow SCH 40)
The dimension parameters of ASTM B363 Grade 2 seamless pipe fittings are as follows:
- 2″ 90° elbow SCH 40:
- Outer diameter (OD) : approximately 50.8 mm
- Inner diameter (ID) : approximately 44.4 mm
- Wall thickness (wall thickness) : about 3.2 mm
- Length : It may vary depending on the application, but it is usually around 1000 mm
- 4″ 90° elbow SCH 40:
- Outer diameter (OD) : approximately 101.6 mm
- Inner diameter (ID) : approximately 91.4 mm
- Wall thickness (wall thickness) : about 3.2 mm
- Length : It may vary depending on the application, but it is usually around 1000 mm
These parameters comply with the requirements of ASTM B363 and are suitable for the manufacturing and application of titanium and titanium alloy pipe fittings.
ASME B16.9 and MSS SP 43 standards for pipe fitting dimensions
The requirements for pipe fitting dimensions of ASME B16.9 and MSS SP 43 standards are as follows:
- Size range :
- ASME B16.9 standard is suitable for pipe systems from NPS 1/2 to NPS 48 (DN 15 to DN 1200) including various types of welded joints such as right angle elbows, reducer elbows, tees and reducer tubes. .
- The MSS SP 43 standard is mainly suitable for stainless steel butt welded pipe fittings, ranging in size from 1/2 inch to 24 inch (DN15 to DN600), and covers short pipes and pipe ends for use with Schedule 5S, 10S and 40S pipes.
- Dimensional tolerance :
- ASME B16.9 standard specifies tolerances for the outer diameter, inner diameter, wall thickness and overall length of pipe fittings. For example, for NPS 1/2 to NPS 24 fittings, the tolerance for outer and inner diameters is ±0.03 inches and the tolerance for wall thickness is ±0.05 inches.
- The dimensional tolerances of the MSS SP 43 standard are basically the same as those of ASME B16.9, but the tolerances of the outer diameters vary under different sizes. For example, for NPS 1/2 to NPS 5 fittings, the tolerance for outer diameter is ±0.03 inches; for NPS 6 to NPS 20 fittings, the tolerance for outer diameter is ±0.05 inches; for NPS 21 to NPS 40 fittings, the tolerance for outer diameter is ±0.05 inches; for NPS 21 to NPS 40 fittings, the tolerance for outer diameter is ±0.05 inches; for NPS 21 to NPS 40 fittings, the tolerance for outer diameter is ±0.05 inches; The tolerance of the diameter is ±0.08 inches.
- Wall thickness :
- The ASME B16.9 standard allows negotiation between the manufacturer and the purchaser to determine the wall thickness, but the wall thickness should not be less than 87.5% of the nominal wall thickness.
- The MSS SP 43 standard also allows the manufacturer and purchaser to negotiate to determine the wall thickness, but the specific values must comply with the provisions of ASME B36.19.
- Shape requirements :
- The ASME B16.9 standard specifies the shape requirements of pipe fittings, including outer diameter, inner diameter, end preparation, corner preparation and concentricity.
- The MSS SP 43 standard also stipulates the shape requirements of pipe fittings, but mainly focuses on stainless steel butt welded pipe fittings to ensure consistency with ASME B16.9 standard.
- Materials and Grades :
- The ASME B16.9 standard is suitable for a variety of materials, including carbon steel, alloy steel, duplex stainless steel and non-ferrous metals.
- The MSS SP 43 standard is mainly suitable for stainless steel materials and complies with ASTM A347, A234 WPB and other standards.
To sum up, the ASME B16.9 and the MSS SP 43 standards have similarities in terms of dimension range, dimensional tolerance, wall thickness, shape requirements and material grade, but the specific details and scope of application are different. The ASME B16.9 standard is more extensive and is suitable for a wide range of materials and sizes, while the MSS SP 43 standard focuses more on stainless steel butt welded fittings.
Specific requirements of titanium alloy pipe fittings raw material standard (ASTM B348/B265/B381/B861/B862)
The specific requirements of the titanium alloy pipe fittings raw material standard (ASTM B348/B265/B381/B861/B862) are as follows:
- ASTM B265:
- Suitable for titanium and titanium alloy strips, plates and plates.
- The chemical composition and mechanical properties requirements of different grades of titanium and titanium alloys are specified.
- Chemical components include the maximum or minimum content of elements such as nitrogen, carbon, hydrogen, oxygen, vanadium, aluminum, zirconium, ruthenium, tungsten, palladium, cobalt, chromium, nickel, niobium, boron, etc.
- Mechanical performance requirements include tensile strength, bending test, etc.
- Dimensional tolerances, surface roughness, packaging and marking are also specified in detail.
- ASTM B348:
- Suitable for titanium and titanium alloy rods and blanks.
- The chemical composition, mechanical properties and heat treatment requirements of different grades of titanium and titanium alloys are specified.
- Chemical components include the maximum or minimum content of elements such as nitrogen, carbon, hydrogen, oxygen, vanadium, aluminum, zirconium, ruthenium, tungsten, palladium, cobalt, chromium, nickel, niobium, boron, etc.
- Mechanical performance requirements include tensile strength, yield strength, elongation and hardness.
- Dimension and shape tolerances, surface roughness, product packaging and markings are also specified in detail.
- ASTM B381:
- Suitable for casting ingots of titanium and titanium alloys.
- The chemical composition and mechanical properties requirements of different grades of titanium and titanium alloys are specified.
- Chemical components include the maximum or minimum content of elements such as nitrogen, carbon, hydrogen, oxygen, vanadium, aluminum, zirconium, ruthenium, tungsten, palladium, cobalt, chromium, nickel, niobium, boron, etc.
- Mechanical performance requirements include tensile strength, yield strength and elongation.
- Dimension and shape tolerances, surface roughness, product packaging and markings are also specified in detail.
- ASTM B861:
- Suitable for titanium and titanium alloy seamless pipes.
- The chemical composition and mechanical properties requirements of different grades of titanium and titanium alloys are specified.
- Chemical components include the maximum or minimum content of elements such as nitrogen, carbon, hydrogen, oxygen, vanadium, aluminum, zirconium, ruthenium, tungsten, palladium, cobalt, chromium, nickel, niobium, boron, etc.
- Mechanical performance requirements include tensile strength, yield strength and elongation.
- Dimension and shape tolerances, surface roughness, product packaging and markings are also specified in detail.
- ASTM B862:
- Suitable for titanium and titanium alloy welding pipes.
- The chemical composition and mechanical properties requirements of different grades of titanium and titanium alloys are specified.
- Chemical components include the maximum or minimum content of elements such as nitrogen, carbon, hydrogen, oxygen, vanadium, aluminum, zirconium, ruthenium, tungsten, palladium, cobalt, chromium, nickel, niobium, boron, etc.
- Mechanical performance requirements include tensile strength, yield strength and elongation.
- Dimension and shape tolerances, surface roughness, product packaging and markings are also specified in detail.
These standards ensure the performance and quality of titanium alloy pipe fittings in different application fields and are suitable for aerospace, medical, chemical, marine and other industries. Specific material standards may vary according to the country and region. It is recommended to choose applicable standards based on actual application.
Technical specifications for manufacturing technology of titanium alloy pipe fittings (forging/extrusion/welding, etc.)
The manufacturing process of titanium alloy pipe fittings includes various methods such as forging, extrusion and welding, each method has its own specific technical specifications and requirements. Here is a detailed description of these processes based on the information I searched for:
1. Forging technology
Forging is one of the key steps in the manufacturing of titanium alloy pipe fittings. The specific steps are as follows:
- Smelting : Vacuum consumable arc smelting or electron beam smelting technology is usually used to ensure uniformity and high purity of alloy composition.
- Heating : Heat the ingot to a specific temperature, usually 900~950℃.
- Forging : Perform multiple forgings on the press, including upsetting, drawing and other operations to improve the structure of the alloy and make it more dense and even.
- Cooling : Annealing is required after forging to eliminate residual stresses generated during processing and stabilize the structure and properties of the material.
2. Extrusion process
Extrusion technology is characterized by high efficiency, high quality, low energy consumption, and less/no cutting process. It is widely used in the production of titanium alloy tubes, rods, profiles and parts. The specific steps are as follows:
- Bill preparation : Heat the forged blank to a certain temperature, usually 750~1300℃.
- Extrusion : Put the blank into the extrusion cylinder, apply pressure through the extrusion rod to extrude the blank out of the die hole of the mold to form a pipe.
- Lubrication : Use lubricants such as glass lubricants to reduce friction and improve extrusion efficiency.
- Cooling : The extruded pipe needs to be annealed to eliminate residual stresses generated during processing and stabilize the structure and properties of the material.
3. Welding process
The welding process is also very important in the manufacturing of titanium alloy pipe fittings, mainly used to connect different parts or repair defects. The specific steps are as follows:
- Material preparation : Ensure that titanium alloy pipes comply with relevant standards and industry specifications.
- Welding method : TiG welding process is adopted to ensure that the welding area is not contaminated by active gases and avoid the occurrence of coarse crystal structure and residual stress.
- Equipment requirements : Use qualified titanium and titanium alloy accessories, welding materials that meet standards (such as welding wire, argon, tungsten electrode), and welding equipment (such as welding machines, welding torches, argon conveying pipes, etc.).
- Welding parameters : including tungsten electrode diameter, welding wire diameter, welding gun diameter, voltage, current, time, interlayer temperature, nozzle flow, argon flow, protective atmosphere flow, etc.
- Quality control : The welding process needs to be strictly controlled, including appearance inspection, X-ray inspection, color inspection and hardness testing.
4. Technical Specifications
- National Standard : GB/T 26058-2010 “Titanium and Titanium Alloy Extruded Pipes” stipulates the requirements, testing methods, inspection rules, etc. of titanium and titanium alloy extruded pipes.
- Industry Standard : GB/T 26057-2010 “Titanium and Titanium Alloy Welded Pipes” stipulates the requirements, testing methods, inspection rules, etc. of titanium and titanium alloy welded pipes.
- Other standards : such as GB/T 2822 “Metal Materials Room Temperature Tensile Test Method”, GB/T 241 “Metal Tube Hydraulic Test Method”, etc.
5. Other precautions
- Chemical composition : The chemical composition of titanium alloy pipes shall comply with the provisions of GB/T 3620.1, and the allowable deviation shall comply with the provisions of GB/T 3620.2.
- Dimensional tolerance : The allowable deviation of the outer diameter of the pipe shall comply with the provisions of Table 1, and the allowable deviation of the wall thickness shall not be higher than ±12.5% of its nominal wall thickness.
- Surface quality : The surface of the pipe must not have cracks, folds, deep grooves, oxide scales or other defects.
To sum up, the manufacturing process of titanium alloy pipe fittings involves multiple links, and each step requires strict control and optimization to ensure the quality and performance of the final product.
Effect of stress-relieving annealing on the performance of titanium alloy pipe fittings
The impact of stress-relieving annealing on the performance of titanium alloy pipe fittings is mainly reflected in the following aspects:
- Changes in mechanical properties :
- After stress relief annealing, the tensile strength and yield strength of TC18 titanium alloy will decrease, but its impact toughness, fracture toughness and elongation will increase. This shows that annealing treatment can effectively reduce residual stress and improve the plasticity and toughness of the material.
- In the study of TA18 titanium alloy pipes, as the insulation time is extended, the strength of the material is slightly reduced, but the elongation is improved. This shows that the annealing treatment can improve the ductility of the material by eliminating residual stress.
- Changes in microstructure :
- Stress elimination and annealing will cause changes in the microstructure of titanium alloy pipe fittings, grain refinement, and dislocation density to decrease. These changes help improve the toughness and plasticity of the material.
- In the study of TC4 titanium alloy, after annealing, there were more biphasic structures in the BM region, and after annealing, the α phase in the BM region became more diverse and the α phase structure was more uniform. This tissue change helps to improve the overall performance of the material.
- Residual stress elimination :
- Stress relief annealing can significantly reduce residual stress in titanium alloy fittings. Residual stress removal helps prevent deformation or cracking of the material during subsequent use.
- In the study of TA18 titanium alloy pipes, as the insulation time is extended, the residual stress is gradually released, and the degree of softening of the material increases.
- Effects of fatigue performance :
- Stress elimination annealing has a significant impact on the fatigue performance of titanium alloy pipe fittings. In the study of TC4 titanium alloy self-punching riveting parts, stress relief annealing can improve the fatigue performance of riveting parts, especially within the medium life range.
- However, vibration stress elimination (VSR) has a negative impact on the fatigue life of Ti-6Al-4V titanium alloy, and the fatigue life decreases as the VSR amplitude increases.
- Impact of other performance :
- Stress elimination and annealing can improve the welded joint performance of titanium alloy pipe fittings. In the study of TC4 titanium alloy electron beam welding joints, the tensile strength and elongation of the base material under the stress annealing state are higher than that of the fully annealed state.
- In the study of laser repair of TC18 titanium alloy forging parts, after annealing treatment, the mechanical properties of the repair area gradually returned to the specified value of TC18 forging parts.
To sum up, the impact of stress elimination annealing on the performance of titanium alloy pipe fittings is mainly reflected in mechanical properties, microstructure, residual stress and fatigue properties. Through reasonable selection of annealing parameters, the comprehensive performance of titanium alloy pipe fittings can be effectively improved and meet the needs of different application scenarios.
You must be logged in to post a comment.