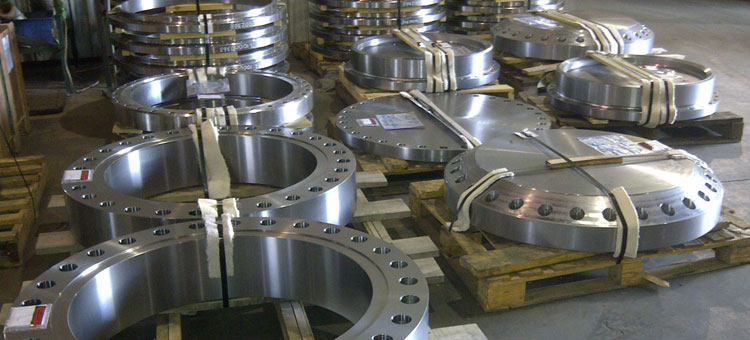
Introduction
Duplex stainless steels such as ASTM A 182 F51 standardized under UNS designation S31803 have gained widespread adoption in heat exchangers and piping systems where high strength, corrosion resistance, and cathodic protection are demanded. This report analyzes key aspects of S31803 flanges including metallurgy, mechanical properties, performance factors, specification requirements, inspection methods, and future trends relevant for designers and fabricators to optimize reliability.
Microstructure and Phase Balance
The defining characteristic of duplex alloys lies in their microstructure comprising approximately equal proportions of both austenite and ferrite phases, as opposed to a single-phase microstructure found in austenitic or ferritic steels. In S31803, chromium (~23%) and molybdenum (~3.5%) stabilize the phases while nickel (~4-5%) raises the ferrite-to-austenite transformation temperature. Small additions of nitrogen further promote austenite formation via interstitial solution strengthening. This dual-phase nature imbues significantly higher strength than austenitic alloys yet doubles the corrosion resistance of ferritics.
Mechanical Properties
Table 1 lists typical mechanical properties of S31803:
Property Value
Yield Strength (ksi) 65
Tensile Strength (ksi) 90
% Elongation 30
Hardness, HRC 25-30
Compared to carbon steel flanges, S31803 offers nearly 3x greater yield strength and a balanced strength-toughness profile. The duplex phase structure prevents strain-induced martensite transformation allowing uniform deformation. These attributes enable cost savings through reductions in size, wall thickness, and joint weights.
Corrosion Resistance
S31803’s corrosion properties originate from high chromium and molybdenum contents which form a tightly-adherent, self-healing protective chromium oxide film. This affords broad application ranges, including:
General corrosion and chloride environments up to 150°C
Sour gas/H2S service if inhibited below 60°C
Resistance to pitting and crevice corrosion via passive film repassivation
Additionally, S31803’s ferrite matrix facilitates cathodic protection through galvanic coupling with active sacrificial anodes. Together, its dual-phase structure and composition confer enhanced resistance exceeding austenitic alloys in many industrial fluids.
Fabrication and Standards
Flanges manufactured from S31803 extrusions or forgings undergo rigorous welding, heat treatment and inspection controls to realize optimal properties while averting damage mechanisms. Key specifications are:
ASTM A182/ASME SA-182 establishes chemical composition ranges
ASTM A960 guides welding procedures and filler metal selection
AMS-5827 covers fabrication and heat treatment practices
NACE MR-0175/ISO 15156 governs corrosion-resistant alloy use in oil/gas
ASME B16.5 dictates pressure ratings, dimensions and stamping marks
Compliance ensures each flange possesses consistent metallurgy free from welding defects to perform dependably under service extremes.
Performance Evaluation and Monitoring
Since S31803 is susceptible to stainless steel damage like sensitization, a multi-tiered evaluation program confirms as-built condition and detects any degradation over time:
Dye-penetrant testing checks for surface-connected imperfections post-fabrication
Ultrasonic inspection quantifies residual wall thicknesses compared to nominal
Electrochemical testing evaluates passive film integrity and risk of corrosion
Stress corrosion cracking samples expose flanges to cracking environments
Cathodic protection surveys monitor current, potential to sustain film repassivation
Data from these non-destructive examinations quantifies remaining life thereby supporting risk-informed asset management replacing components before failure.
Future Prospects
Research advances duplex alloy development to realize:
Higher alloy content grades extending temperature/pressure capabilities
Additions of copper improving localized corrosion resistance
Powder metallurgy routes for net-shape manufacturing complex geometries
Coatings inhibiting microbiologically-influenced corrosion and deposits
Non-destructive techniques coupling acoustic emissions/guided waves for earlier flaw detection
Meanwhile, process simulations optimize heat treatments lowering manufacturing costs. With optimized standards and characterization techniques, next-generation duplex alloys will continue providing high-performance flanges assuring equipment reliability far into the future.
Conclusion
This analysis reviewed the microstructure, properties and performance attributes establishing S31803/ASTM A182 F51 duplex stainless steel as an important class of flanges engineered for demanding services. Future prospects center around addressing remaining metallurgical challenges or expanding working limits through advanced alloys. Combined with strategic qualification, fabrication and monitoring practices, duplex flanges offer durable, economical and cathodically-protected connectivity supporting process operations.
You must be logged in to post a comment.