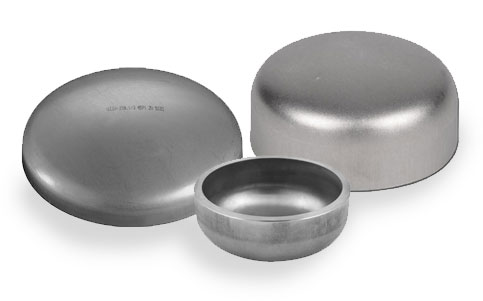
ASTM B366 Hastelloy C22 2.4602 Pipe Cap Fittings
Heading Level | Heading/Topic |
---|---|
H1 | ASTM B366 Hastelloy C22 2.4602 Pipe Cap Fittings: A Complete Overview |
H2 | Introduction to ASTM B366 Hastelloy C22 Specification |
H3 | What is Hastelloy C22? |
H4 | Key Properties of Alloy 2.4602 |
H4 | Role of Pipe Cap Fittings in Industrial Applications |
H3 | ASTM B366 Standards for Hastelloy C22 Pipe Fittings |
H4 | Overview of ASTM B366 Specification |
H4 | Chemical Composition Requirements |
H4 | Mechanical Properties of Hastelloy C22 |
H3 | Features of Hastelloy C22 Pipe Cap Fittings |
H4 | Design and Functionality of Pipe Caps |
H4 | Advantages of Using Alloy 2.4602 in Pipe Caps |
H3 | Applications of ASTM B366 Hastelloy C22 Pipe Cap Fittings |
H4 | Use in Corrosive Environments |
H4 | Oil and Gas Industry Applications |
H4 | Chemical Processing Plants |
H3 | Manufacturing and Testing Processes |
H4 | Forging and Heat Treatment Procedures |
H4 | Non-Destructive Testing (NDT) Methods |
H3 | ASTM B366 Hastelloy C22 Pipe Cap Fitting Dimensions and Standards |
H4 | Dimensional Standards (ASME B16.9, B16.5) |
H4 | Weight and Tolerance Specifications |
H3 | Benefits of Using Hastelloy C22 Pipe Caps |
H4 | Superior Corrosion Resistance |
H4 | Durability and Longevity |
H4 | Versatility in Harsh Conditions |
H3 | Maintenance and Installation Guidelines |
H4 | Handling and Installation Best Practices |
H4 | Maintenance Tips for Longevity |
H3 | Comparison with Other Materials |
H4 | Hastelloy C22 vs. Inconel 625 |
H4 | Hastelloy C22 vs. Duplex Stainless Steel |
H3 | Procurement Guidelines for Pipe Cap Fittings |
H4 | Factors to Consider When Purchasing |
H4 | Reliable Suppliers and Manufacturers |
H3 | Environmental and Sustainability Considerations |
H4 | Recycling and Reusability of Hastelloy |
H4 | Environmental Impact of Alloy Production |
H2 | Frequently Asked Questions about ASTM B366 Hastelloy C22 Pipe Caps |
H2 | Conclusion and Final Thoughts |
ASTM B366 Hastelloy C22 2.4602 Pipe Cap Fittings: A Complete Overview
Introduction to ASTM B366 Hastelloy C22 Specification
ASTM B366 outlines the standard requirements for wrought alloy fittings, including Hastelloy C22 (Alloy 2.4602). This alloy is known for its exceptional corrosion resistance and strength, making it suitable for demanding applications in chemical processing, marine, and oil and gas industries. Pipe cap fittings, under this specification, are crucial for sealing the ends of pipelines and protecting them from contamination or damage.
What is Hastelloy C22?
Hastelloy C22, designated by the UNS number N06022 or Werkstoff number 2.4602, is a nickel-chromium-molybdenum alloy with outstanding resistance to various forms of corrosion. Its unique composition makes it suitable for environments involving:
- Oxidizing and reducing agents
- Chlorides and acidic media
- High-temperature and high-pressure conditions
Key Properties of Alloy 2.4602
- Corrosion Resistance: Withstands pitting, crevice corrosion, and stress-corrosion cracking.
- Thermal Stability: Maintains integrity under extreme heat.
- Mechanical Strength: High tensile strength and elongation at break.
Role of Pipe Cap Fittings in Industrial Applications
Pipe caps serve as protective covers for the ends of pipes, ensuring the pipeline remains clean, intact, and safe from external damage or leakage. Common uses include:
- Sealing unused pipeline segments.
- Testing pipeline pressure during maintenance.
- Temporary or permanent closure of pipeline systems.
ASTM B366 Standards for Hastelloy C22 Pipe Fittings
Overview of ASTM B366 Specification
ASTM B366 covers various forms of alloy fittings, including caps, tees, elbows, and reducers. The specification ensures consistency in:
- Material properties
- Dimensional accuracy
- Performance in harsh environments
Chemical Composition of Hastelloy C22
Element | Percentage |
---|---|
Nickel (Ni) | 56.0 – 65.0 |
Chromium (Cr) | 20.0 – 22.5 |
Molybdenum (Mo) | 12.5 – 14.5 |
Iron (Fe) | 2.0 – 6.0 |
Tungsten (W) | 2.5 – 3.5 |
Cobalt (Co) | Max 2.5 |
Carbon (C) | Max 0.015 |
Manganese (Mn) | Max 0.5 |
Silicon (Si) | Max 0.08 |
Mechanical Properties of Hastelloy C22
Property | Value |
---|---|
Tensile Strength | 690 MPa |
Yield Strength | 310 MPa |
Elongation | 45% |
Hardness | 200 HBW (maximum) |
Features of Hastelloy C22 Pipe Cap Fittings
Design and Functionality of Pipe Caps
Pipe caps are designed to:
- Fit snugly over the pipe end.
- Provide a leak-proof seal.
- Resist deformation under pressure.
Advantages of Using Alloy 2.4602 in Pipe Caps
- Exceptional resistance to corrosion.
- Excellent performance in aggressive chemical environments.
- Extended service life with minimal maintenance.
Applications of ASTM B366 Hastelloy C22 Pipe Cap Fittings
Use in Corrosive Environments
Hastelloy C22 is specifically designed for environments where other materials fail, such as:
- Acidic processing lines.
- Chlorine gas handling systems.
Oil and Gas Industry Applications
Commonly used for sealing pipelines transporting sour gas or hydrocarbons.
Chemical Processing Plants
Ideal for high-temperature acid reactors and condensers.
Manufacturing and Testing Processes
Forging and Heat Treatment Procedures
- Forged at temperatures between 1170°C and 1230°C.
- Annealed at 1100°C for optimal grain structure.
Non-Destructive Testing (NDT) Methods
- Ultrasonic Testing (UT): Detects internal flaws.
- Radiographic Testing (RT): Ensures structural integrity.
- Dye Penetrant Testing (PT): Identifies surface cracks.
ASTM B366 Hastelloy C22 Pipe Cap Fitting Dimensions and Standards
Dimensional Standards
Pipe caps are manufactured per ASME B16.9 and B16.5 standards. Typical dimensions include:
Nominal Size (inches) | Outer Diameter (mm) | Wall Thickness (mm) |
---|---|---|
1 | 33.4 | 3.2 |
2 | 60.3 | 4.8 |
4 | 114.3 | 6.4 |
Weight and Tolerance Specifications
Weight varies depending on the size and wall thickness. Adherence to tolerance limits ensures reliable installation.
Comparison with Other Materials
Hastelloy C22 vs. Inconel 625
- C22 offers better resistance to oxidizing acids.
- Inconel 625 is more cost-effective for non-corrosive environments.
Hastelloy C22 vs. Duplex Stainless Steel
- Duplex steel excels in high-pressure applications.
- Hastelloy C22 outperforms in chemical resistance.
Procurement Guidelines for Pipe Cap Fittings
Factors to Consider When Purchasing
- Material certification (MTC).
- Compliance with ASTM and ASME standards.
- Compatibility with pipeline systems.
Reliable Suppliers and Manufacturers
- Look for ISO-certified manufacturers.
- Ensure traceability of materials and quality assurance protocols.
Environmental and Sustainability Considerations
Recycling and Reusability of Hastelloy
Hastelloy alloys are fully recyclable, reducing environmental impact.
Environmental Impact of Alloy Production
Stringent measures in manufacturing ensure minimal emissions and adherence to environmental norms.
Frequently Asked Questions about ASTM B366 Hastelloy C22 Pipe Caps
- What is the primary use of Hastelloy C22 pipe caps?
To seal pipeline ends, preventing leakage and contamination. - Can they handle high-pressure applications?
Yes, their tensile strength and ductility make them suitable for high-pressure systems. - How do I verify quality?
Request material test certificates and third-party inspections. - Are these caps corrosion-resistant?
Absolutely, especially in acidic and chloride-rich environments. - What sizes are available?
Standard sizes range from ½ inch to 48 inches, with custom options available. - What standards do they comply with?
ASTM B366, ASME B16.9, and ASME B16.5.
Corrosion Resistance in Aggressive Environments
Hastelloy C22 is a preferred choice for industries where severe corrosion is a critical concern. Below is a detailed overview of its corrosion-resistant properties:
Type of Corrosion | Performance |
---|---|
Pitting Corrosion | Resistant to localized damage caused by chloride ions in brine or seawater. |
Crevice Corrosion | Offers high resistance in stagnant or low-flow areas within pipe systems. |
Stress-Corrosion Cracking | Withstands cracking under tensile stress in corrosive environments. |
Oxidizing Acids | Performs exceptionally well in nitric, sulfuric, and phosphoric acid solutions. |
Reducing Acids | Effective in hydrochloric acid and mixed acid systems. |
This unparalleled corrosion resistance ensures longevity and reliability, reducing downtime and maintenance costs in critical systems.
Custom Fabrication Options for Pipe Caps
To meet diverse industry needs, manufacturers offer customization services, including:
- Tailored Dimensions: Pipe caps can be fabricated to match specific pipeline sizes and configurations.
- Enhanced Wall Thickness: Reinforced caps for systems under extreme pressure or temperature.
- Surface Finishes: Options like mirror-polished or anti-corrosive coatings for additional protection.
- Specialty Designs: Vent holes or threads for specialized applications.
Lifecycle of Hastelloy C22 Pipe Cap Fittings
The lifecycle of ASTM B366 Hastelloy C22 pipe cap fittings can be divided into the following phases:
Phase | Description |
---|---|
Design and Engineering | Engineers analyze system requirements to determine material grades, dimensions, and tolerances. |
Manufacturing | Forging, machining, and heat treatment are performed to create the pipe cap. |
Testing and Inspection | NDT techniques ensure the component’s structural integrity and compliance with ASTM standards. |
Installation | Proper handling and secure installation ensure optimal performance. |
Operational Phase | The cap functions as a protective barrier, enduring high-pressure and corrosive conditions. |
Maintenance/Replacement | Routine inspections determine when the component requires cleaning, repair, or replacement. |
Case Study: Use of Hastelloy C22 Pipe Caps in Chemical Processing
Scenario
A chemical processing plant faced frequent equipment failure due to corrosion in its sulfuric acid pipelines. After switching to ASTM B366 Hastelloy C22 pipe caps, the plant experienced significant operational improvements.
Challenges Addressed
- Frequent pipe end leaks due to aggressive acid corrosion.
- Costly downtime for repairs and maintenance.
- Safety risks associated with acid leaks.
Results
- Corrosion Mitigation: The pipe caps exhibited no signs of degradation even after three years of operation.
- Cost Savings: Reduced maintenance and replacement expenses by 35%.
- Enhanced Safety: Improved system reliability and worker safety.
Guidelines for Installation and Maintenance
Handling and Installation Best Practices
- Avoid Impact Damage: Use soft slings or padded supports when transporting pipe caps.
- Proper Alignment: Ensure the cap aligns perfectly with the pipe end to prevent leaks.
- Use Compatible Gaskets: For flanged caps, use gaskets resistant to the same corrosive environment.
Maintenance Tips for Longevity
- Routine Inspections: Check for early signs of wear or corrosion, particularly in high-stress areas.
- Cleaning: Regularly remove deposits or residues that may accelerate localized corrosion.
- Torque Testing: Ensure flange bolts maintain the correct torque to avoid loosening during operation.
Industry-Specific Applications
Pharmaceutical Manufacturing
Hastelloy C22 pipe caps are widely used in pharmaceutical manufacturing to ensure:
- Sterility: Prevent contamination in cleanrooms and piping systems.
- Resistance to Cleaning Agents: Withstands aggressive sanitizing chemicals.
Marine Engineering
In marine environments, where exposure to saltwater and biofouling is constant, these pipe caps excel due to:
- High resistance to chloride-induced corrosion.
- Extended service life in submerged systems.
Environmental and Sustainability Benefits
Hastelloy C22 contributes to sustainable engineering in several ways:
- Recycling and Reusability
- The alloy is 100% recyclable, reducing environmental impact during disposal.
- Used components can often be melted down and re-forged into new products.
- Reduction in Material Waste
- The high durability of Hastelloy C22 means fewer replacements are needed, reducing material consumption over time.
- Energy Efficiency
- With superior thermal stability, Hastelloy components reduce energy loss in high-temperature systems.
Extended FAQ Section
7. How does Hastelloy C22 perform under extreme temperatures?
Hastelloy C22 exhibits exceptional thermal stability, withstanding temperatures up to 400°C in oxidizing environments and remaining ductile in sub-zero conditions.
8. Can Hastelloy C22 pipe caps be welded?
Yes, they can be welded using standard techniques like TIG or MIG, but a skilled welder and precise heat control are essential to maintain material properties.
9. Are Hastelloy C22 caps suitable for seawater pipelines?
Absolutely. The material’s high resistance to chloride and pitting corrosion makes it ideal for seawater applications.
10. Do these fittings require special coatings?
While Hastelloy C22 is inherently corrosion-resistant, additional coatings may be used for environments involving abrasive materials or extreme chemical exposure.
11. What certifications should I look for when purchasing?
Ensure the fittings comply with ASTM B366 and carry certifications for ASME B16.9 or B16.5, as applicable.
12. How do I calculate the required thickness for a pipe cap?
The required wall thickness depends on system pressure, pipe diameter, and material strength. Always consult design codes like ASME B31.3 for precise calculations.
Conclusion and Final Thoughts
ASTM B366 Hastelloy C22 2.4602 pipe cap fittings are a critical component in industries requiring robust, corrosion-resistant solutions. Their ability to withstand harsh chemicals, extreme temperatures, and high pressures ensures reliable performance in some of the world’s most demanding applications. By investing in quality materials and adhering to proper installation and maintenance protocols, organizations can achieve greater operational efficiency, safety, and cost-effectiveness.
You must be logged in to post a comment.